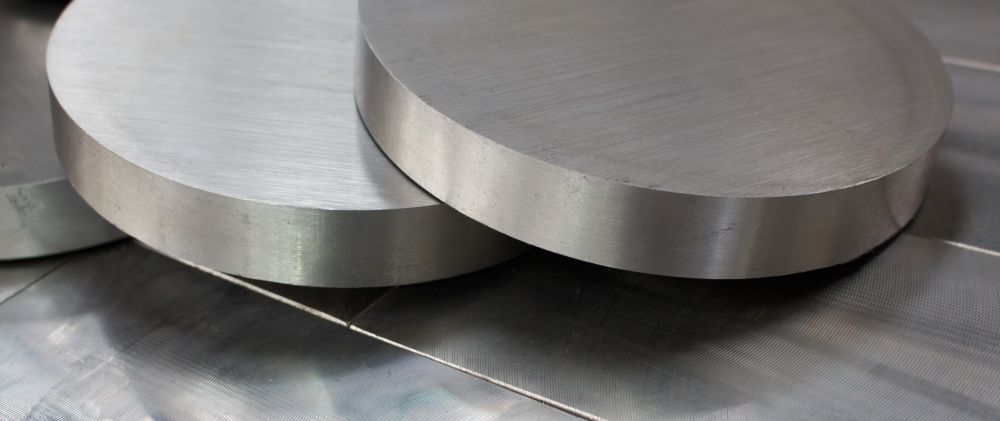
Yüksek performanslı östenitik paslanmaz çelik (HPASS), paslanmaz çeliklerle elde edilebilecek en yüksek korozyon direncini sağlar. Her alaşım farklı özelliklere sahip olsa da, hepsi korozyon performansının üç ana alanından birinde veya daha fazlasında göze çarpmaktadır: genel korozyon, oyuklaşma ve aralık korozyonu ve stres korozyonu çatlaması.
HPASS üzerindeki pasif film molibden ile güçlendirilir. Buna rağmen, olumsuz çevresel koşullar altında parçalanabilir ve korozyonun başlamasına izin verir. Geniş film bozulması, tüm yüzeyde korozyona neden olur (genel korozyon). Lokalize film bozulması, oyuk korozyonu oluşturur. Molibden varlığı nedeniyle, HPASS üzerindeki film bozulmaya standart derecelere göre daha dayanıklıdır.
Malzeme mühendisi, pasif filmi ilgili ortamda koruyacak en uygun maliyetli paslanmaz çelik derecesini seçmelidir. Üretici ve kullanıcı, zayıf imalat veya çalışma koşulları nedeniyle alaşımın temel direncini azaltan faktörleri anlamalıdır. Bu bölüm paslanmaz çelik korozyon direncine ilişkin bazı temel ilkeleri sunmaktadır.
Önerilen Makale: Çelik sac malzemeler ve uygulamaları hakkında detaylı bilgi almak için
paslanmaz çelik sac sayfamızı ziyaret etmenizi tavsiye ederiz.
Genel Korozyon
Genel korozyon, enine kesitte eşit incelme sağlayan yüzeyden homojen bir metal kaybıdır. Paslanmaz çeliklerde genellikle güçlü, sıcak asitlerde bulunur. Genel korozyon genellikle ortamın seçilen kalite için çok agresif olduğunu gösterir. Ortam oksitleniyorsa, daha fazla krom içeren bir kalite genellikle daha iyi performans verecektir. Ortam azalıyorsa, daha yüksek krom, nikel, molibden ve bakır içeren kaliteler daha iyi performans gösterir. Küçük miktarlardaki kirlenme, hizmet ortamlarının saldırganlığını önemli ölçüde değiştirerek, nispi oksitlenme veya azaltma güçlerini etkileyebilir. Bu tür değişiklikler paslanmaz çeliğin korozyon performansını da etkileyebilir.
Bölgesel Korozyon
Çukur ve Çatlak Korozyonu
Çukurlaşma ve çatlak korozyonu, metalin yüzeyinde lokalize bir alanda meydana gelir. Pasif filmin yerel olarak bozulmasının birçok yolu vardır, bu nedenle bu korozyon formları meydana gelme olasılığı en yüksektir. Tanım olarak, çukurlaşma nispeten temiz, kusursuz bir yüzeyde gerçekleşir. Aralık çatlaması bir aralıkta meydana gelir - örneğin bir cıvatanın veya skalanın altında. Bu tür korozyon özellikle tehditkardır, çünkü görünüşte iyi huylu bir ortamda ortaya çıkarlar ve bir kez başlatıldığında çok hızlı bir şekilde nüfuz edebilirler.
Lokalize saldırılara karşı direnç, HPASS'taki bu alaşım eklemelerinin büyük miktarını oluşturan daha yüksek Cr, Mo ve N içeriğiyle artar. Çukurlaşma ve çatlak korozyonunu destekleyen çevresel koşullar arasında halid iyonları (özellikle klorür), manganez gibi oksidanlar, yüksek sıcaklıklar ve genel saldırı üretmek için yeterince agresif olmayan asit koşulları bulunur. Zararlı tasarım veya çalışma koşulları, cıvatalı bağlantılar gibi yerleşik çatlakları ve ölçekli yüzeyler gibi zayıf sistem temizliği ile ilgili birikintileri içerir. Dikkatsiz imalat uygulamaları, korozyonu başlatan kirli veya lekelenmiş yüzeyler oluşturarak yerel korozyonu da teşvik edebilir. Bazen, zayıf iç çelik temizliği ve bazı istenmeyen metal olmayan kapanımlar veya metaller arası fazlar lokal korozyonu çekirdeklendirebilir.
HPASS, belirli bir maliyet ve üretilebilirlik gereksinimleri kümesi için mümkün olan en yüksek oyuk ve çatlak korozyon direncini sağlar. Yüksek korozif çözeltilerdeki laboratuvar çukurluğu ve çatlak korozyon testleri, göreli direnç için farklı alaşımları sıralamak ve geliştirilmiş alaşımların geliştirilmesine yardımcı olmak için kullanılır. Bu testlerin çoğu, belirli bir test ortamı koşulları seti için sıralama kriteri olarak sıcaklığı kullanır. Sıralama kritik oyuk sıcaklığı (CPT) veya kritik aralık sıcaklığı (CCT) olarak ifade edilir. Kritik sıcaklık, sıcaklık arttıkça korozyonun oluşmaya başlayacağı sıcaklıktır (bu nedenle daha yüksek bir kritik sıcaklık, düşük bir sıcaklıktan daha iyidir). Belirli bir alaşımın CCT'si her zaman CPT'den daha düşüktür çünkü çatlak korozyonu, çukur korozyonundan daha kolay başlar.
Sıralama testleri ve sonuçtaki kritik sıcaklıklar, bir alaşımın belirli bir ortamda nasıl performans göstereceğini ayrıntılı olarak tahmin etmez, ancak daha yüksek CCT veya CPT'ye sahip alaşımlar genellikle bir dizi gerçek ortama göre daha iyi korozyon direncine sahiptir. Saha deneyimi kritik sıcaklıklar ve saha performansı arasında bazı genel korelasyonlara izin verir. ASTM G48 CPT değeri 10 °C (50 °F) olan 316L tipi, deniz suyunda buhar yoğunlaştırıcı tüp servisi için uygun değildir. CPT 75 °C (167 °F) olan HPASS alaşımı 254 SMO, bu ortamda tatmin edici hizmet vermektedir.
Sekonder Fazların Lokalize Korozyon Üzerine Etkisi
Östenitik paslanmaz çelikler tek fazlı alaşımlar olmakla birlikte, her zaman çelik üretiminin normal sonucu olan diğer küçük fazları içerirler. Mevcut fazlar, eriyik atölyesinde çelik rafine etme uygulamasından oksit ve sülfür inklüzyonları, katılaşma sırasında faz ayrılmasından kaynaklanan ferrit ve tavlama veya kaynak sırasında oluşabilecek karbür, chi ve sigma fazlarını içerir. Bu fazlar çelik yüzeydeki süreksizlikleri temsil eder ve pasif filmi bozdukları için oyuk veya çatlak korozyonunu kolaylaştırabilirler. Turşu ve pasivasyon tedavileri genellikle yüzeyden çıkarılır ve etkilerini en aza indirir.
Bununla birlikte sigma ve chi fazları oluştuğunda, bazı durumlarda problem oluşturabilirler. Çeliğin ilk katılaştırılması sırasında alaşım elemanı ayrışmasından kaynaklanırlar ve ayrıca Bölüm 3.3'te tartışıldığı gibi tavlama veya kaynak gibi sonraki ısıl işlemler sırasında da oluşabilirler. Çok miktarda krom ve molibden içerdiklerinden, çevreleyen alanı alaşım elementlerinde tüketir ve korozyon direncini azaltırlar. Çelik üretimi sırasında oluşurlarsa, genellikle zararlı değildirler, müteakip haddeleme ve tavlama işlemleri yapıyı homojenize eder ve metaller arası fazları çözer. Ancak, atölye kaynağı veya tavlama sırasında oluşurlarsa, çok zararlı olabilirler.
Stres Korozyon Kırılması
Çoğu alaşımda, stres ve spesifik ortamın kombinasyonu, stres korozyonu çatlaması (SCC) olarak bilinen bir tür korozyona neden olacaktır. Bu korozyon şekli genellikle tane sınırlarına nüfuz eden dar dallanma çatlakları olarak ortaya çıkar. Paslanmaz çeliklerde, bu genellikle klorür içeren ortamlarda gerçekleşir ve klorür stres korozyon çatlaması (CSCC) olarak adlandırılır.
SCC'nin meydana gelmesi için, spesifik aşındırıcı ortamla birlikte bir çeşit çekme gerilimi mevcut olmalıdır. Stresin kaynağı, üretim süreçleri nedeniyle servis stresleri veya artık stres olabilir. Artık gerilmeler sıklıkla oldukça yüksek olduğundan, bunlar SCC'de sıklıkla bir faktördür. 304 ve 316 Tipleri dahil olmak üzere standart östenitik paslanmaz çelikler bu korozyon formuna karşı çok hassastır. HPASS buna oldukça dayanıklıdır.
Klorür Stres Korozyon Kırılması (CSCC)
CSCC tavlanmış bir östenitik paslanmaz çelikte meydana geldiğinde, stres paterni tarafından belirlenen bir morfolojiye sahip transgranüler çatlaklar sergiler. Duyarlılık, SCC duyarlılığını arttırır ve taneler arası çatlamayı teşvik eder. Yüksek stres, yüksek sıcaklık, yüksek klorür ve düşük pH, stres korozyonu çatlaması olasılığını artırır. Şekil 15, 304 ve 316 Tipleri için mevcut CSSC verilerinin bir özetini sunar. Nötr sularda, bu alaşımlarda kaynamaya yakın veya daha yüksek sıcaklıklarda çatlama üretmek için gereken klorür içeriği 1 ppm'den azdır. Daha düşük sıcaklıklarda, ortamın yakınında, stres korozyon hataları yine de ortaya çıkacaktır, ancak biraz daha yüksek klorür seviyelerinde - 1-10 ppm ve üstü aralığında. İzolasyon altındaki alternatif ıslak / kuru yüzeyler gibi klorürleri yoğunlaştıran koşullar, nominal ortam sadece birkaç ppm klorür içerdiğinde bile CSCC'ye neden olabilir.
304 ve 316 Tipler'in% 8-12 aralığının üzerinde nikel içeren östenitik paslanmaz çeliklerin hepsi önemli ölçüde daha iyi CSCC performansı sağlar. Daha yüksek krom ve molibden içeriklerinden ve daha yüksek nikelden yararlanan HPASS, özellikle CSCC'ye dirençlidir. Örneğin, UNS N08367 (AL-6XN) alaşımında, çatlama çok daha yüksek sıcaklık ve klorür seviyelerine kadar başlamaz. Sıcaklık eşikleri 100 °C'nin (212 °F) çok üzerindedir, bu da atmosfer basıncında kaynar nötr klorür çözeltilerinin% 6 Mo ve benzer HPASS'de çatlama üretme olasılığının düşük olduğunu, 304 ve 316 Tiplerinde önemli bir gelişme olduğunu gösterir.
Diğer Ortamlarda Gerilme Korozyonu Çatlaması
Güçlü kostik ortamlar, kostik çatlama adı verilen paslanmaz çeliklerde bir tür stres korozyonu oluşturur. 304 ve 316 tipleri ve diğer benzer standart kaliteler, yaklaşık 100 °C (212 °F) veya daha yüksek sıcaklıklarda hassastır. Nikelin arttırılması kostik çatlama direncini arttırır, bu nedenle tüm HPASS standart kalitelerden daha iyi performans gösterir. Bununla birlikte, 150 °C'ye (300 °F) yaklaşan çok agresif ortamlarda çalışan kostik evaporatörler gibi uygulamalar için sadece Ni bazlı alaşımlar yeterli hizmet sağlar.
Yüksek hidrojen aktivitesine sahip ortamlar, "hidrojen gevrekleşmesi" olarak adlandırılan bir çeşit çatlak üretebilir. Bu ortamlar arasında yüksek basınçlı hidrojen gazı, güçlü asitler, hidrojen sülfit gibi bir katalizör içeren asit çözeltileri ve elektrokaplama çözeltileri bulunur. Tüm standart östenitik ve HPASS kaliteleri, martensit içerebilen Tip 301 gibi metastabil kaliteler hariç, bu çatlamaya karşı oldukça dirençlidir. Bununla birlikte, aşırı soğuk olan herhangi bir kalite, mukavemeti ve sertliği arttırmak için savunmasızdır. NACE Standard MR0175 ve ISO 15156, onaylı kaliteler ve kabul edilebilir sertlik hakkında ayrıntılı bilgi sağlar.
Poliiyonik asit (H2S406) ayrıca hassaslaşmış östenitik paslanmaz çelikte SCC üretebilir. Uygun termal işlemlere tabi tutulan 304 ve 316 Tipleri veya 321 ve 347 Tipleri gibi hassasiyete dayanıklı kalitelerin kullanılması bu tehlikeyi önleyecektir. Bununla birlikte, bu dereceler bile hassaslaştırma aralığında uzun süreli maruz kaldığında duyarlı hale gelebilir ve duyarlı hale gelebilir. HPASS, politiyonik asit içindeki standart kalitelerden biraz daha iyi performans gösterir.
Taneler Arası Korozyon (IGA) / Hassaslaştırma Korozyonu
Taneler arası korozyon, tahıl sınırlarında çok az veya hiç saldırı olmaksızın tahıl sınırları içinde veya yakınında hızla meydana gelir. Standart östenitik paslanmaz çelikler için, bu saldırı modu genellikle kaynak veya ısıl işlem sırasında meydana gelen duyarlılaşma ile ilişkilidir. Duyarlılık derecesine ve çevrenin korozivitesine bağlı olarak, korozyon birden fazla form alabilir. Duyarlılık orta derecede ise çukurluk atağı muhtemeldir. Tane sınırları boyunca sürekli bir krom karbür ağı mevcutsa, korozyon tanecikler arası olarak ortaya çıkar ve korozyon yüzeyden düşen tanelerle genel korozyona benzeyecektir. Gerilme gerilimi varsa SCC benzeri bir korozyon meydana gelebilir.
Tasarımcılar ve imalatçılar, hassaslaşmayı ve bunun sonucunda oluşan taneler arası saldırıyı en aza indirmek için üç seçeneğe sahiptir:
Düşük bir karbon derecesi kullanın (örn. Tip 304L, 316L veya 317L). Düşük karbon içeriği, soğutma sırasında krom karbür çökeltme başlamadan önce geçen süreyi uzatır. Bu, sıcak imalat teknikleri, kaynak ve ağır tavlanmış bölümlerin kullanılmasını mümkün kılar. L kalitelerinin kullanılması, çeliğin kritik hassaslaştırma sıcaklık aralığında uzun süreli hizmete maruz kalması sırasında hassasiyete dayanacağı anlamına gelmez.
Dengeleyici bir katkı maddesinin karbonu bağladığı stabilize edilmiş bir östenitik sınıf kullanın. İki yaygın katkı maddesi titanyum (Ti) ve niyobyum / columbium'dur (Nb / Cb). Bu kaliteler, tercihen krom karbür yerine titanyum veya niyobyum / columbium karbür oluşturan uygun bir stabilize edici ısıl işlem gerektirir.
Çözelti, korozyon direncini geri kazanmak için önceden hassaslaştırılmış malzemeyi tavlar. Önerilen çözelti tavlama sıcaklıkları 1030-1175 °C (1900-250 °F) arasındadır. Çözelti tavlama işlemi, bileşen tarafından görülen son termal işlem olmalıdır. Hizmetteki yüksek sıcaklıklara maruz kalan bileşenler için uzun süreli duyarlılık tehlikesini ortadan kaldırmaz.
HPASS, genellikle krom karbür hassasiyetinin endişe verici olmamasını sağlamak için yeterli azot içeren düşük karbonlu alaşımlardır. Bununla birlikte, daha önce tartışıldığı gibi, bu alaşımlarda standart derecelerde duyarlılık üretenlere benzer termal koşullar altında intermetalik fazlar oluşabilir. Bu olursa, çelik agresif bir ortama maruz kaldığında hızlandırılmış oyuk korozyonu olası korozyon sonucudur.
Kaynak Hassasiyeti / Kaynak Bozulması
Kaynak, metalin bir süre boyunca kaynak içinde ve yakınında duyarlılık sıcaklığı aralığında olmasına neden olur. Kaynağın çeliğe duyarlı olup olmadığı alaşıma, kesit kalınlığına ve ısı girdisine bağlıdır. Şekil 16, tipik bir kaynak termal döngüsünü ve kaynak bozulmasına duyarlı ilişkili bölgeyi şematik olarak göstermektedir. Şekilde, kaynağın her iki tarafında oluşan hassaslaştırılmış bir malzeme bandı gösterilmektedir. Kaynak bozulması, kaynak koşullarının kontrol edilmesi ve hassasiyet kontrolü için daha önce tartışılan üç yaklaşımdan biri veya daha fazlası kullanılarak en aza indirilir. HPASS genellikle kaynak sırasında krom karbür hassasiyetine maruz kalmaz. Bununla birlikte, kaynak termal döngüleri, çukurlaşma direncini bozan metaller arası bileşiklerin oluşumunu teşvik edebilir. Kaynak parametreleri kritik sıcaklık aralığında süreyi en aza indirmeli ve çoklu kaynak geçişlerinden kaçınılmalıdır.
İmalat ve Korozyon Direnci Arasındaki İlişkiler
Bu bölüm öncelikle korozyonu etkileyen metalürjik ve çevresel faktörleri ele almıştır. Bununla birlikte, basit imalat kayıplarının çoğu alan korozyon probleminin nedeni olduğunu söylemek güvenlidir. Paslanmaz çelik, korozyon direnci sağlamak için iyi, güçlü bir pasif filme bağlıdır. Ne yazık ki, birçok standart imalat işlemi pasif filmi olumsuz etkileyebilir. Yüzey koruyucu filme zarar veren herhangi bir şeyin korozyon direncini azalttığını unutmamak önemlidir. İki geniş hasar kategorisi tanımlanabilir: yüzey durumu ve yüzey kontaminasyonu. Yüzey durumu, tümü bileşene özgü olan pürüzlülüğü, artık gerilmeyi ve yüzey alaşımı tükenmesini içerir. Yüzey kontaminasyonu, yüzeye verilen yabancı bir maddedir ve bileşen için dışsaldır. Kontaminantların listesi uzundur, ancak bazı yaygın olanlar klorür içeren işaretleme boya kalemleri veya çözücüleri, aletlerden demir kirlenmesi ve tavlama veya kaynak ölçeğidir. Bölüm 7 ve 14, bu konular hakkında daha fazla tartışma ve imalatçıların etkilerini ortadan kaldırmaları veya en aza indirmeleri için öneriler sunar.
Neyse ki, imalat problemleriyle ilişkili korozyon, nedenlerini anlayarak ve bunları ortadan kaldırmak için dikkatli adımlar atılarak önlenebilir. Bu genellikle iyi temizlik prosedürleriyle birlikte iyi temizlik anlamına gelir.