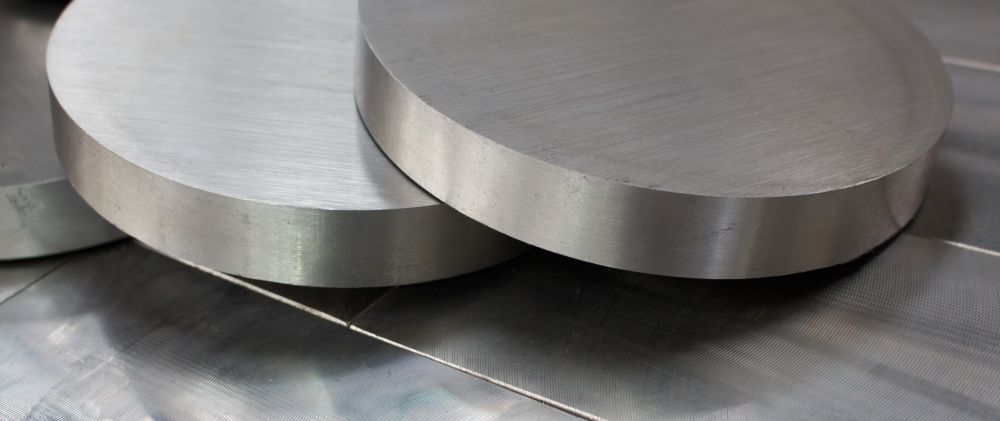
Takım ağzı kızaracak ölçüde yüksek kesme hızlarında dahi talaş kaldırabilen, yani bu koşullara rağmen yüksek sıcaklık sertliğini büyük oranda ve uzun süre koruyan malzemelerdir. Söz konusu özelliklerin çeliğe kazandırılabilmesi için belirli alaşım elementlerinin katılması, özenli eritme (elektrik ocağı), karbürlerin homojen dağılımını sağlayacak şekilde sıcak haddeleme ve kullanıcı tarafından malzemeye uygun bir ısıl işlem programının gerçekleştirilmesi zorunludur.
Yüksek hız çeliklerinin kesme kabiliyetinin kızıl sıcaklıkta bile çok iyi olması, içyapılarında öncelikle volfram, krom, molibden, vanadyum elementlerinin oluşturduğu özel karbürlerin büyük miktarda bulunmasından ileri gelir. Bu nedenle karbon oranı da en az % 0,8 dolayında veya daha fazladır. Yumuşatılmış durumdaki kararlı karbürlerin su vermeden önce yeteri kadar çözünmesi gerektiğinden, ostenitleme sıcaklığı solidüs çizgisinin hemen altında (1200°C ... 1320°C) seçilir. Öte yandan tane irileşmesine yol açmamak için sıcaklık ve tutma süresine kesin şekilde uyulmalıdır. Çarpılma ve çatlamayı önlemek üzere, bu malzemeler iki veya üç kademede ve çoğunlukla tuz banyosunda ısıtılırlar. Sertleştirmeden sonra çeliğin içyapısı yaklaşık %70 martenzit, %10 karbür ve %20 artık ostenitten meydana gelir. 550°C dolayında yapılan temperleme ile önceden çözünmüş olan özel karbürlerin yeniden oluşturulup ince dağılmış biçimde çökeltilmesi sertlikte büyük bir artış sağlar ikincil sertleşme). Temperlenen martenzitin ferrit ve Fe
3C benzeri karışık karbürlere ayrışması sertlik düşüşüne neden olurken, çökelme ile elde edilen bu sertlik kazancı yüksek hız çeliklerine özgü temper davranışını ortaya çıkarır.
Temperlemede karbürler sadece martenzitten değil artık ostenitten de ayrışır. Böylece karbon ve alaşım elementi miktarı azalarak Ms sıcaklığı yükselen artık ostenitin, soğuma sırasında büyük ölçüde (temperlenmemiş) martenzite dönüşmesi yeniden temperlemeyi gerektirebilir. Temperlemede, yayınmaya bağlı oldukları için olaylar çok yavaş gelişir. Dolayısıyla çoğu durumda ve öncelikle temperlenmemiş martenzit oranı yüksekse iki veya üç kez temperleme yapılır. Yüksek hız çeliklerinde son olarak vurgulanması gereken nokta, işletme sıcaklığı arttıkça -özellikle temperleme sıcaklığının üzerinde (>550°C)- sertliğin zamanla azalmasıdır.
ASTM A600-79 standardı tanımına göre yüksek hız takım çelikleri, yüksek hızda kesim yapabilme kapasitesine sahip takım malzemesi olarak tanımlanan çelik türüdür. Bu takım çeliğinin gelişimi oldukça uzun bir kronolojiye sahiptir.
Yüksek hız takım çeliklerinin, takım çelikleri içinde sınıflandırılmaya başlaması bugünün klasik yüksek hız takım çeliklerinden sayılan T1 (18W-4Cr-1V) malzemenin, 1910 yılında kullanıma girmesiyle olmuştur. İlk üretilen hız çeliğinden günümüze takım çeliğinin geliştirilmesi konusunda oldukça gelişmeler yaşanmış ve 20m/dk hızlarından, bugün PVD ile TiN kaplanmış, toz metal hız çeliklerinde 120m/dk‘ya kadar ilerlenmiştir. Bu takım çeliği türündeki gelişmeler zaman içinde yaşanan alaşım elementlerinin bulunamaması (Mo ve Co) durumlarında çeşitlilik kazanmış ve alaşım elementleri ile sınıflandırılması geliştirilmiştir. Her bir alaşım elementinin etkisi bu süreçte daha iyi anlaşılmış ve bu alaşım elementlerinin kombinasyonlarının sonuçları ve homojenlikleri incelenmiştir. Bu konuda tabii ki en büyük gelişme toz metalurjik üretimin başlamasıyla olmuştur.
Yüksek hız takım çeliklerinin alaşım elementlerine ve uygulanan ısıl işlem özelliklerine göre mikroyapılarının ve mekanik özelliklerinin kontrol edilmesi sonucu belirgin özellikler ve dizaynlar elde edilmiş ve bu şekilde sertlikle birlikte tokluğun gerekli olduğu kullanım alanlarında tercih edilir olmuştur. Öncelikle kullanım alanı olarak kesme ve delme işleri olmak üzere bitirici işlemlerden delik genişletmede, broşlamada, diş açmada, azdırmada, şekillendirmede ve traşlamada kullanılmaktadır. Bunun dışında çok sayıda farklı operasyonda ihtiyaç duyulan ince uçlu bıçaklarla kağıt, ağaç ve yiyecek kesme işlemlerinde bu çelik türü tercih edilmektedir.
AISI standardına göre yüksek hız takım çeliklerini kırktan fazla çeşitte sınıflandırma yapılabilmektedir. Yalnız AISI ‘nın genel olarak kabul gören sınıflandırması oldukça eski zamandan beri kabul gören tungsten ve molibden içeriğine göre sınıflandırmadır.
Önerilen Makale: Paslanmaz sac malzemeler ve uygulamaları hakkında detaylı bilgi almak için
paslanmaz sac sayfamızı ziyaret etmenizi tavsiye ederiz.
Tungstenli Yüksek Hız Takım Çelikleri
Bu sınıfta yer alan yüksek hız takım çeliği genel olarak yapısında tungsten, krom, vanadyum, kobalt ve karbon içermektedir. AISI standardına göre bu
sınıftaki çelikler T ile gösterilmektedir. İlk üretilen yüksek hız takım çeliği olan T1 çeliğinde de günümüzdeki alaşım miktarlarına yakın bir analiz vardır. Sadece vanadyum miktarının ve karbon miktarının artışı son otuz yıllık periyotta olmuştur.
%1,5 vanadyum ve %1 karbondan daha yüksek değerlerde alaşım elementi içeren bu yüksek hız takım çeliği, yüksek alaşımlı yapısı sayesinde mikroyapısında oldukça sert karbürler bulundurmaktadır. Ayrıca bu sınıftaki çeliklerin yüksek sıcaklıklarda da sertliğini muhafaza etmesinden ötürü çok çeşitli takımlarda, takım elemanı olarak kullanımı yaygındır. Bu nedenle kesme kalıpları, punçlar, broşlar ve yüksek sıcaklıkta çalışan havacılık sektöründe burç yatağı olarak kullanıma uygundur.
T tipi yüksek hız takım çeliklerinin tamamı yüzeyden çekirdeğe kadar havada sertleşebilen çelik sınıfındadır. Östenitleme sıcaklığından havada soğutulmaya bırakılan bir T tipi yüksek hız takım çeliği 76 mm.’lik kalınlıklara kadar ki boyutlarda maksimum sertlik değerlerini göstermektedir.
Molibdenli Yüksek Hız Takım Çelikleri
Bu sınıfta yer alan yüksek hız takım çeliği genel olarak yapısında molibden, tungsten, krom, vanadyum, kobalt ve karbon içermektedir. AISI standardına göre M simgesi ile gösterilmektedir. Bu sınıftaki yüksek hız takım çelikleri T sınıfından farklı olarak daha yüksek tokluk değerlerine sahiptir. Bu özellik dışında iki yüksek hız takım çeliği için mekanik özellikler oldukça benzerdir.
Yüksek alaşımlı yapısı sayesinde sıcakta sertliğini kaybetmeye direnci oldukça iyidir. Yalnız bu sınıftaki çeliklerin daha yüksek hassasiyet isteyen bir östenitleme koşulları vardır. Çünkü T tipi yüksek hız takım çeliklerinin daha yüksek östenitleme koşulları, M tipi için üst limitlerin de ötesine geçmektedir.
Bu sınıftaki hız çelikleri, içerdikleri alaşım oranına bağlı olarak 62 HRC sertlik değerinden 65 HRC sertlik değerlerine hatta M40 hız çeliğinde ise 66-68 HRC sertlik aralığına ulaşılmaktadır.
Toz Metalurjik Yüksek Hız Takım Çelikleri
Toz metalurjik yüksek hız takım çelikleri üstün performansı ve üretim kolaylığı nedeniyle matkap uçları, broşlar ve çeşitli kesici takım malzemesi olarak kullanılmaktadır. Geleneksel yöntemle üretilen yüksek hız takım çeliklerine göre çeşitli avantajlara sahiptir:
• Segregasyon olmadan ingot üretiminin mümkün olması
• İnce taneli mikroyapıya sahip üretimin yapılması
• Tüm yapıda homojenliğe sahip olması
• Yüksek tokluğa sahip olması
• Üstün parlatılabilirlik kabiliyetine sahip olması
• Tane boyutu kontrol edilebilir olması
• Homojen sertlik değerleri göstermesi
Toz metalurjik yöntemle üretimde, atomizasyon yoluyla hızla soğutularak üretilen tozlar kullanıldığından segregasyon riski ortadan kalkmaktadır. Ayrıca karbürler ve metalik olmayan inklüzyonlarla çok ince ve homojen bir mikroyapı elde edilir. Toz metalürjisinin yüksek hız takım çeliği üretimine dahil olmasıyla, hız çeliklerinde son özellikler bakımından kayda değer gelişmeler olmuştur. Bunlar tokluk, ısıl işlemde boyut kontrolü, parlatılabilirlik ve zorlu koşullarda kesim performasıdır. Ayrıca bu yöntemle alaşım miktarında kısıtlama olmamaktadır. Böylece istenen özellikleri arttırmaya yönelik yüksek alaşımlı çeliklerin üretimi mümkün olmuştur.
Toz metalurjik yöntemle 1970 yılından günümüze çok çeşitli üretim yöntemleri geliştirilmiştir. Son olarak günümüzde yaygın olarak kullanılan yöntem ise, gaz atomizasyon ile tozun üretimi ve bunu takip eden izostatik presleme yöntemiyle üretimdir.
Anti-Segregasyon Prosesi (ASP1), toz metalurjik üretim için geliştirilmiş bir yöntemdir. Bu yöntemde ergitilmiş metale inert bir gaz üflenerek küresel yapıda toz elde edilmektedir. Daha sonrasında tozlar silindirik metal çerçevelere yerleştirilip uzun süre titreşime tutulur. Böylece silindir içerisinde tüm yapının homojen olması sağlanır. Daha sonrasında metal çerçevenin üstü kaynakla kapatılır. Bu kapsül önce soğuk izostatik sonra sıcak izostatik presleme işlemine tabii tutulur ve tüm yoğunluğunu alması sağlanır. Daha sonrasında üretilen toz metalurjik hız çeliği sıcakta dövme veya haddeleme ile istenen boyutlara indirilir.
Yüksek Hız Takım Çeliklerinin Özellikleri
Yüksek hız takım çelikleri tür ve üretim yönteminden bağımsız olarak aşağıda sıralanmış şu ortak özelliklere sahiptir:
• Hepsi yüksek alaşımlıdır.
• 64 HRC sertlik değerine ulaşacak kadar karbon içeriğine sahiptir.
• Üstün sertleşebilirlik kabiliyeti sayesinde çekirdekten yüzeye kadar homojen sertlik dağılımına sahiptir.
• Yüksek östenitleme sıcaklığından havada soğutma ile maksimum sertlik değerlerinde sertlik almaktadır.
Bütün yüksek hız takım çelikleri yapısında ön tavlanmış karbür partikülleri içermektedir. Bu karbür partikülleri hız çeliğinin aşınma direncine katkıda bulunmaktadır. Isıl işlem esnasında belli bir kısmı çözünerek matrikse geçen alaşım elementleri çeliğin sertleşebilirliğini arttırmaktadır.
Tüm hız çelikleri benzer mekanik ve fiziksel özellikler gösterse de alaşım elementleri oranları değiştirilerek farklı çalışma koşulları için farklı özellikler gösterebilmektedir. Bir yüksek hız takım çeliğinden beklenen en önemli özellik bu çeliğin kesme kabiliyetidir. Kesme kabiliyeti için dört önemli özellik gerekmektedir.
• Sertlik
• Sıcak
• Sertlik
• Aşınma Direnci
• Tokluk
Bu dört özelliğin öncelik sıralaması sadece kullanım yerinde ihtiyaç duyulma oranına göre yapılmaktadır. Hız çeliğinin alaşımlandırılması da kullanım alanındaki ihtiyaç önceliğine göre yapılmaktadır.
Sertlik: Bütün yüksek hız takım çeliklerinde en çok aranan özelliktir. Oda sıcaklığında yüksek hız takım çeliklerinin 64 HRC sertlik alabilir olması gerekmektedir. Bazı takım çelikleri (M40, T15) ise 69 HRC ve daha yüksek sertliklere çıkabilmektedir.
Sıcak Sertlik: Kesme kabiliyetinin göreceli olarak en önemli özelliklerinden biridir. Çünkü kullanım alanında sürtünme ile artan sıcaklıklarda kesici uç sertlik değerlerini kaybetmektedir. Bu özelliğin önemine göre yüksek hız takım çeliğinin kimyasal kompozisyonuna kobalt eklenmektedir.
Aşınma Direnci: Yüksek hız takım çeliğinin kesme kabiliyetine etki eden üçüncü önemli özelliği ise aşınma direncidir. Kesici takımın performansı aşınma yüzeyinin incelenmesi ile olmaktadır. Kesici takım için performans sağlayacak mikroyapının geliştirilmesi için aşınmanın mekanizması bilinmelidir. Genel olarak kesici takımlar için ana aşınma mekanizması abrasiv aşınmadır. Bu tür aşınmada temel, kesici ucun mikrosabanlama yapıyor olmasıdır. Kesim esnasında oluşan talaşın ortamdan uzaklaşmaması durumunda talaş, kesici ucu ikinci kez aşındırmaktadır. Hem kesici takımın ömrü azalmakta hem de kesilen yüzeyin kalitesi düşmektedir. Bu nedenle kesim esnasında yeterli miktarda ve temiz bir kesme sıvısı ortama besleniyor olmalıdır.
Yüksek hız takım çeliğinden yapılan bir kesici takım malzemesi yukarıda açıklanan durum gereğince mikro-sabanlamaya karşı koymalıdır. Aksi takdirde elmasların kesici
köşelerinin mikro-kırılmalar yaşayarak körelmesi ile karşı karşıya kalınacaktır. Çalışma sırasında kesici takım sürekli aşınmakta ve yüzeyin altında gömülü karbürler sırayla yüzeye çıkarak kesme işini devam ettirmektedir. Eğer matriks yumuşak kalırsa karbürler yüzeyden erken kopmaktadır. Yalnız sadece sertliğin yükseltilmesi de aşınma direnci bakımından yeterli değildir. Çünkü sert matriks bu karbürlerin de görev değişimine engel olacaktır. Körelen karbür yüzeyden kopamayacak ve alttan yeni karbür gelemeyecek olması takımın hızını azaltacaktır. Bu nedenle matriks sertliği ömür uzatıyorsa belirli bir oranda da kesme hızını düşürdüğü bilinmelidir.
Tokluk: Kesme kabiliyeti için gerekli olan dördüncü özelliktir ve toplamda iki ana faktörden oluşmaktadır:
• Kırılmadan önceki şekil değiştirme yeteneği
• Kalıcı şekil değişikliğine karşı direnci
Yüksek hız takım çeliğine daha çok uyan durum ise elastik deformasyon direncidir. Kesici uç olarak üretilmiş yüksek hız takım çeliği darbe görmekte ve bu darbeleri adsorbe edebilme yeteneğine sahip olmalıdır.
Çeliklerde Karbür Oluşumu ve Özellikleri
Karbürler hem metalik bağlantı karakteri hem de kimyasal bağlantı karakteri taşıdığından oldukça karmaşık yapılardır. Demir içinde yer alan karbürlerin türü elementlerin periyodik tablodaki yeri ile ilgilidir. Buna bağlı olarak da karbürlerin kararlılığı belirlenmektedir.
Demirde karbür elementi ile bir başka element daha karbür içinde yer alabilir. Bu durumda karbür toplam 3 elementten meydana gelebilmektedir. Bu nedenle de karbürlerden genel olarak bahsedilirken karbür içinde yer alan tüm elementler hakkında bilgi sahibi değilsek genel gösterimi kullanabiliriz. M3C, M7C3 ve M23C6 gibi örnekler verilebilir. Aşağıdaki tabloda periyodik tablodaki sistematiğe uygun karbürlerin bağlantıları yer almaktadır.
Karbonca zengin olan karbürlerin yapıları oldukça basittir. Yukarıdaki tabloda da IV. ve V. grup karbürleri olarak görülmektedir. Genellikle kübik kafes şeklinde ve karbon atomu ara yer şeklinde olandır. Bu karbür tipine örnek olarak, TiC, ZrC, VC, NbC gösterilebilir. Yalnız karbon atomu bütün boşlukları dolduramadığından bu yapı içerisine atom çapları nispeten küçük olan diğer elementler girebilmektedir. Bunlara örnek olarak azot ve oksijen atomları sayılabilmektedir. Zaten nitrür tabakalarında görülen, karbonitrür, oksikarbonitrür ve oksikarbürler de bu şekilde meydana gelmektedir. Bu nedenle sitokiyometrik olarak vanadyum karbür gibi kararlı değillerdir.
Hekzagonal yapıda olan karbürler bu sınıflandırmada ayrı bir basamak oluşturmaktadırlar. Bu yapı içerisinde oldukça kararlı olan karbürler de bulunmaktadır. MC ve MC2 konsantrasyonlarındadır. Bu yapı içerisinde karbon atomları oktaedrik ara hacimde, metal düzlemleri arasındadır.
Karbürler içerisinde en az stabiliteye sahip bir diğer grup ise genelde krom elementinin karbürü olarak bilinen M7C3 karbürleridir. Bu karbürlerin östenit içerisindeki stabilitesi diğer iki gruba göre daha düşüktür. Çözünebilirliği ise daha yüksektir. Bu karbürlerin kafes yapıları ise ortorombik kristalleridir. Stabilitesi en düşük karbür tipidir ve bu nedenle boyutları ve yapıları benzer bir yabancı atomla karbürdeki element yer değiştirebilmektedir. Özellikle krom elementinin karbür oluşturması konsantrasyona bağlıdır. Buna bağlı olarak krom karbürün çevresinde yüksek miktarda demir atomu bulunmaktadır.
Eğer çeşitli alaşım elementlerinin karbür oluşumuna etkisini özetlersek:
Vanadyum öncelikle MC tipi karbür oluşumunu tetikler. İkinci öncelikte ise diğer karbür tipleri yerine M2C tipi karbür oluşmasına meyillidir.
Molibden M2C tipi karbürleri kararlı kılan elementken, tungstenle birlikte M6C karbürü çökelmesini tetikler.
Krom M7C3 karbürünü kararlı kılar.
Yüksek Hız Takım Çeliklerinde Karbürler
Yüksek hız takım çeliklerinde bulunan karbürlerin malzeme özelliklerine etkisi oldukça yüksektir. Yüksek hız takım çelikleri yüksek alaşımlı takım çelikleri sınıfında yer aldığından bu malzemelerin sıcağa karşı mukavemetleri, yüksek aşınma dirençleri ve kesme kabiliyetlerinin iyi olması bu alaşım elementlerinin oluşturduğu karbürlerin varlığı ile açıklanmaktadır.
Yüksek hız takım çeliklerinde birincil karbürler, çeliğin katılaşması sırasında çökelmektedirler. Genellikle doğrudan sıvı fazdan teşekkülleri söz konusudur. Bu karbürler iki türlü olabilir. Proötektik yapıda olanlar ötektik fazın katılaşmasından önce çökelen karbürler, ötektik yapıda olanlar ise ötektik katılaşması sırasında çökelen karbürlerdir. Buna bağlı olarak proötektik bir karbür yüksek hız takım çeliğinde proötektik dendritlerinde, proötektik östenitte veya delta ferritte yer almaktadır. Ötektik karbürler ise sürekli ağ şeklinde, yapıda ötektik ve interdendritik yapıların içinde veya hücre boşluklarında bulunurlar.
Proötektik karbürler, genellikle saf karbürlerdir. Kimyasal yapıları ise vanadyum ve/veya niyobyum karbür şeklinde olup MC veya M4C3 formlarındadır. Hız çeliğinin yapısına oldukça az miktarda katıldığından, yapıdaki oranları düşüktür. Bu karbürlerde saflık, karbürlerin çökelme sıcaklıkları ile orantılı olduğundan niyobyum karbürün yapısı, vanadyum karbüre göre daha saf olmaktadır. Boyutları 10µm. civarındadır ve sertlikleri 2500 HV’nin üstündedir. Bu yapıdaki proötektik karbürlerin çökelmesi için yapıda bu alaşım elementleri ve yeteri kadar karbon olması şarttır. Genel olarak, takım malzemesi olarak üretilen yüksek hız takım çeliklerinde oluşması beklenen karbürlerdir. Üstün sertlikleri ile bu amaçla üretilen yüksek hız takım çeliklerine yüksek aşınma direnci kabiliyeti ve sertlik kazandırmaktadırlar.
Ötektik karbürler, takım malzemesi olarak tasarlanan yüksek hız takım çeliklerinin dışındaki durumlarda kullanılan karbür türüdür. Bu karbürler ötektik yapı katılaşırken çökmektedirler ve bu nedenle artık interdendritik sıvı içerisinde bulunmaktadırlar. Doğal olarak bu sıvı ile reaksiyon göstermektedir ve üç farklı öteklikte teşekkül eder. Bunlar, ɣ +MC, ɣ +M2C, ɣ +M7C3’tür. Bu ötektik karbürler içerisinde ɣ +MC karbür yapısı ilk olarak çökelen tiptir. Diğer ɣ +M2C ve ɣ +M7C3 karbürlerinin çökelmesi ise sonraki adımlarda gerçekleşmektedir. Bu karbürlerin oluşmasında soğuma esnasında alaşım elementlerinin kimyasal kompozisyon bakımından ayrışması ve soğuma hızı etkilidir. Bu iki karbürden M2C yapısı yüksek tungsten, molibden, vanadyum miktarlarıyla ve hızlı soğuma kapasitesi ile mümkün olmaktadır. M7C3 yapısı ise yüksek krom ve karbon miktarı ile yavaş soğuma oranlarında teşekkül eder.
MC yapısında olan ötektik karbürler, proötektik karbürlerden farklı olarak molibden, tungsten ve krom içerebilmektedir. Ayrıca M6C yapısında olacak kadar genişlemiş türleri demir, tungsten, molibden, vanadyum ve krom içerebilmektedir. Mikroyapısı incelendiğinde çok ince ve düzenli lamelli bir morfolojisi olduğu görülmektedir. Böyle bir karbürün boyutları ise 100 mikron civarında, ancak sertlikleri proötektikden farklı olarak 1100 ile 1500 HV arasındadır. Daha az kompleks M2C yapısında olan türleri de bulunmaktadır. Bunlarda kimyasal farklılık, krom ve molibden miktarının daha yüksek, demir miktarının ise daha düşük olmasıdır. Bu durumda sertlikleri de göreceli olarak yükselmektedir(2000HV). Hız çeliğinde en geniş yapıdaki karbür ise M7C3 karbürüdür ve daha önce bahsedildiği üzere bu karbür krom elementi içermektedir.
Yüksek Hız Takım Çeliklerinde Karbürlerin Özelliklere Etkisi
Karbürlerin özelliklere etkisini incelersek; sertleştirme işleminde çözünmeden kalan karbürlerin malzemenin sertliğini arttırdığı ve buna bağlı olarak kesme kabiliyetini ve aşınma dayanımını büyük ölçüde yükselttiği görülmektedir. Buna bağlı olarak bir takım malzemesine sertlik veren ve abrasiv aşınma direnci sağlayan, karbürlerin miktarı, boyutları ve dağılımıdır. Aşınma direnci ise bu karbürlerin boyutlarından ve boşluklarından etkilenmektedir. Eğer toz metalurjik parçalarda olduğu gibi karbür tanelerinin ve boşluklarının boyutları oldukça benzerse, bu durumda çözünmeden kalan karbür miktarı aşınma direncini belirlemektedir.
Ayrıca ikinci kademede ayrışan karbürlerin hız çeliklerinde, meneviş dayanıklılığı ile sıcakta sertliği yükselttiği görülmektedir.
Karbürlerin yüksek alaşımlı takım çeliklerinde 900⁰C derece ile 1250⁰C derece arasındaki östenitleme sıcaklığında çözünme oranlarını inceleyen bir araştırmada farklı bekleme sürelerinde çeşitli karbür tiplerinin çözünme değerleri tespit edilmiştir. Dokuz adet toz metalurjik olarak üretilmiş D2 soğuk iş takım çeliği üzerinde yapılan çalışmada, 900⁰C, 950⁰C, 1000⁰C, 1050⁰C ve 1100⁰C derecede 20 dakika, 1150⁰C derecede 15 dakika, 1200⁰C ve 1250⁰C derecede 5 dakika östenitleme yapılmıştır. Elde edilen sonuçlar aşağıdaki grafikte yer almaktadır.
Hız çelikleri gibi yüksek alaşımlı çeliklerde karbürü oluşturan elementler yapıda iki şekilde bulunabilir. Bu elementler ya ferritle birlikte sementit içinde yer alırlar ya da ferritle birlikte özel karbür olarak bulunurlar. Karbür içerisinde bulunan elementlerin karbon miktarıyla oranları, karbürün stabilitesini etkilediğinden daha önce bahsedilmiştir. Buna göre karbür oluşturan elementler kesici takım olarak kullanılan hız çeliklerinin yapısı içerisinde yüksek miktarda karbür oluşturan halde; küçük miktarda ise sementite dahil halde bulunmaktadır.
Krom gibi çok farklı şekilde karbürler meydana getirebilen elementler ise yüksek hız çeliği içinde birden fazla karbür tipi oluşturmaktadır. Aynı anda yapı içerisinde aynı elementin farklı karbürleri yer alırsa bu durumda stabiliteye göre karbürlerin çözünme özellikleri görülmektedir. Kromun iki karbürü olan Cr23C6 ve Cr3C2 karbürlerinden Cr3C2 daha kararlı yapıda olduğundan östenitte Cr23C6 karbürü çözünmektedir. Cr3C2 ise çözünmeden kalmaktadır. Çözünen karbürler ise hız çeliklerinin meneviş sıcaklığına denk gelen 450°C - 600°C dereceler arasında tekrar ayrışarak ikincil sertliği oluştururlar.
Yüksek karbon ve yüksek krom içeren soğuk iş takım çeliği sınıfında yer alan 4 numune üzerinde yapılan bir çalışmada, farklı alaşımlı soğuk iş takım çelikleri östenitlenme ve meneviş işlemi görmüştür. Her biri üç meneviş görmüş numunelerin sertlikleri 60 HRC’dir. Daha sonrasında elektron tarama mikroskobu (SEM) kullanılarak mikroyapıları incelenmiştir. Bu mikroskobun ikincil elektron (SE) görüntüleri ve geri saçılan (BE) görüntüleri ile farklı karbürlerin fark edilebilir olması sağlanmıştır. Böyle karbür büyüklükleri, dağılımları ve çeşitleri tespit edilmiştir. Buna göre soğuk iş takım çeliğinde aşınma direnci sağlayan karbürlerin dağılımı aşağıdaki grafikte sunulmaktadır.
Yüksek Hız Takım Çeliklerinde Malzeme Seçim Faktörleri
Yüksek hız takım çeliklerinin en yaygın kullanımı takım malzemesi olduğundan, takımlardan beklenen çeşitli özellikler aynı zamanda yüksek hız takım çeliklerinden de beklenmektedir:
• Yalnızca oda sıcaklığında değil, oda sıcaklığında da takım, iş parçasından daha sert olmalıdır.
• Aralıklı kesme işlemlerinde (freze) görülen mekanik şoklardan (darbeli yüklemelerden) sonra işlevini yürütebilmesi için yeterli tokluğa sahip olmalıdır. Çünkü takımlarda, sert fazlar içeren parçaların talaşlı işlenmesinde dahi mekanik şoklar oluşabilmektedir.
• Takımlar, aralıklı kesme işlemlerinde hızlı ısınma ve soğuma meydana geldiğinden termal şok direncine sahip olmalıdır. Yetersiz olan tokluk ve termal şok direnci, takım ucunda küçük parçaların kopmasına ve hatta takımın kırılmasına neden olur.
• İş parçasına düşük yapışma, bölgesel kaynaklanmayı ortadan kaldırır. Düşük sertlik ve iş parçasına yüksek yapışma, takım şeklinde distorsiyona, takım burnunun kütleşmesine, sertbest yüzey ve krater şeklinde takım aşınmasına neden olduğu için istenmemektedir.
• İş parçası malzemesinde, takım malzemesinin difüzyonu ile hızlı aşınma meydana gelir; bu nedenle iş parçası içinde takımın çözünürlüğü düşük olmalıdır.
Yüksek hız takım çeliklerinin türleri içerisinde tüm kesme faaliyetlerine uygun bir alaşımda malzeme yoktur. Bu nedenle kullanım alanına göre doğru alaşım seçilmektedir. Bunun dışında genel olarak uygulamalarda tercih edilen birkaç tipte yüksek hız takım çeliği bulunmaktadır. Bunlar, molibdenli sınıftan M1, M2, M7 hız çelikleri ile tungstenli sınıftan T1 hız çeliğidir. Bu alaşımlar en yüksek tokluk değerlerine sahip hız çelikleridir. Ayrıca kesim kabiliyeti bakımından üstündürler. Yalnız bu çeliklerin bir dezavantajı, ısıl işlem sonrasında kazandıkları maksimum sertlik değerlerinin diğer yüksek hız takım çeliklerine nazaran düşük olmasıdır.
Yukarıda bahsedilen yüksek hız takım çeliklerinin sertliklerinin göreceli olarak düşük olması nedeniyle sert ve zorlu kesimlerde ömürleri azalmaktadır. Anlaşıldığı üzere aşınma direnci bakımından biraz geride kalmaktadırlar. Bu sorun belirli miktarlarda vanadyum ilavesi sonucunda malzemede bir gelişim sağlamasıyla çözülmektedir. Artan vanadyum miktarına bağlı olarak sertlik yükselmekte ve artan sıcaklıkta sertliğini koruma dayanımı artmaktadır. Bu bakımdan %5 V içeren yüksek hız takım çeliği olan T15 daha yüksek sertlik değerlerine sahip olmakta, alüminyum, paslanmaz çelik, refrakter malzemeleri gibi sert malzemelerin kesilmesinde kullanılmaktadır.
Dövme yüksek vanadyumlu hız çelikleri ise toz metalurjik üretilmiş hız çeliklerine nazaran daha zor parlatılabildiğinden bu konuda da yüksek vanadyumlu hız çelikleri yerine toz metalurjik hız çelikleri tercih edilmektedir.
Yüksek kobalt alaşımlı hız çelikleri artan sıcaklıklarda sertliklerini muhafaza ettiklerinden, sıcak sertliğin istenildiği durumlarda öncelikli olarak tercih edilmelidir. Sıcak sertlik dayanımının miktarları artan kobalt alaşım miktarıyla orantılıdır. Fakat artan kobalt miktarı hız çeliğinin kırılganlığını da arttırmaktadır. Bu nedenle kullanım alanında tercih edilirken, yeterince sert malzeme kesileceğinden ve malzemenin kesinlikle ısınıp ısınmayacağından emin olmak gerekmektedir.