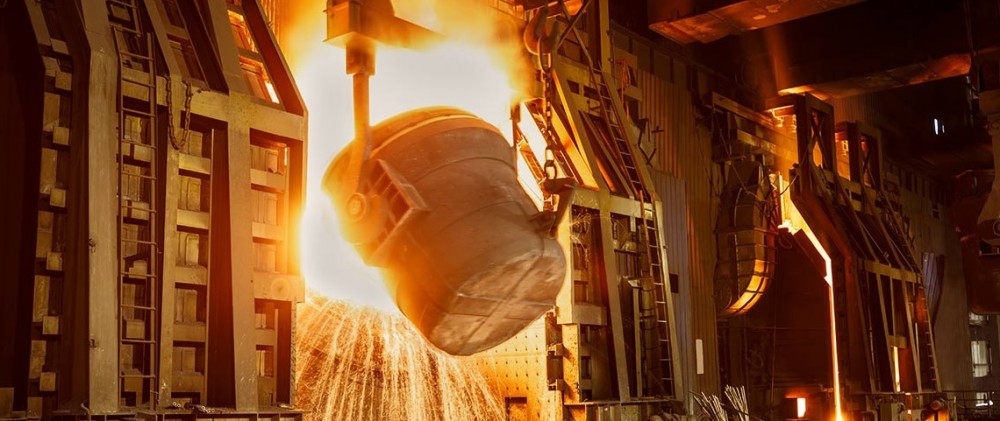
Döküm, işlenmemiş malzemelerin kullanılabilir parçalara dönüştürülmesinin en kolay yoludur. Bununla birlikte, geleneksel döküm teknikleri veya yüksek basınçlı kalıp dökümü gibi daha gelişmiş döküm tekniklerinin başlıca sakıncası, gözeneklilik gibi kusurların oluşumudur. Daha da önemlisi, sıcak yırtılmalar, segregasyon kusurları ve bant oluşumu dökülmüş parçaların çalışması esnasında potansiyel çatlak başlangıçları olabilirler. Bu nedenle, bu kusurları gidermek için yeni döküm teknikleri geliştirilmiştir. Çok sayıda kullanılabilir döküm tekniğinden biri olan sıkıştırılmış döküm, daha az kusurlu döküm parçaları yaratmak için daha büyük bir potansiyele sahiptir.
Sıkıştırılmış döküm, katılaşmanın tekrar kullanılabilir bir kalıp içinde yüksek basınç altında tamamlandığı bir üretim tekniğidir. Temelde, erimiş metalin uygulanan hidrostatik basınç altında katılaştığı, kalıp dövme ile kalıcı kalıp dökümü birleştiren bir metal şekillendirme işlemidir. Bu yüksek basınç, geleneksel döküm uygulamalarında erişilen eriyik basınçlarından daha yüksek büyüklüklerdedir. Sonuç olarak, yeni başlamış büzülme gözeneklerinin içine sıcak noktalardan eriyik beslemesi çok kolay bir şekilde sağlanır. Uygulanan yüksek basınç, aynı zamanda eriyik içine gazların girmesini engeller ve hızlı ısı akışı ve ince mikroyapı için döküm ile kalıp arasındaki teması arttırır. Sıkıştırılmış döküm terimi, "basınç kristalleşmesi", "sıvı preslenmesi", "ekstrüzyon dökümü", "sıvı metal dövme işlemi" ve "sıkıştırma şekillendirmesi" gibi birçok eşanlam kazanmıştır.
Sıkıştırılmış döküm, temel olarak hafif ve düşük erime noktalı alüminyum ve magnezyum alaşımlarına uygulanırken, birçok durumda bakır alaşımlarına, dökme demirlere ve çeliklere de uygulanmaktadır. Sıkıştırılmış döküm işlemi, özellikle kompozitler alanında gelişmiş malzemelerin üretimi için yeni fırsatlar sağlamıştır. Sıkıştırılmış döküm ile üretilmiş metal matris kompozitlerine ilişkin çok sayıda yayım bulunmaktadır. Sıkıştırılmış döküm aynı zamanda bi-metallerin üretimi için de kullanmaktadır, burada örneğin dökme demir takviyeleri alüminyum alaşımlarında aşınma direncini arttırmak için dahil edilmektedir. Uygulamaları; jantlar, pistonlar ve fren diskleridir.
Ayrıca sıkıştırılmış dökümde geri çekilebilir kenar maçalar kullanılarak boylu boyunca boşluklar yapmak da olasıdır.
İşlem Sırası
Sıkıştırılmış döküm için temel olarak işlem sırası şu şekildedir:
1. Önceden belirlenmiş miktarda iş malzemesinin ergitilmesi, düzeneğin bütün temas yüzeylerinin yağlanması ve düzeneğin ön ısıtılması.
2. Doğrudan veya besleme yolundan geçerek kalıp boşluğu içine sıvı metalin boşaltılması.
3. Kalıbın kapatılması ve katılaşma tamamlanana kadar basınç uygulanması. Bu işlem hem ısı akış hızını artım hem de makro/mikro büzülme gözenekliliğini azaltır. Çünkü gaz gözenekliliğinin çekirdeklenmesi basınç bağımlıdır ve gözenek oluşumu erimiş metal içinde tutulan erimiş gazlara bağlıdır.
4. Dökümün çıkarılması, düzeneğin temizlenmesi ve ocağın yeniden şarj edilmesi.
Önerilen Makale: Çelik profil malzemeler ve uygulamaları hakkında detaylı bilgi almak için
kutu profil sayfamızı ziyaret etmenizi tavsiye ederiz.
Sıkıştırılmış Dökümün Sınıflandırılması
Sıkıştırılmış döküm işlemi, basıncın doğrudan erkek kalıptan (ıstampa) geçerek, katılaşan döküm ürünü üzerine uygulanması veya uygulanan basıncın orta seviyedeki bir besleme sistemi üzerinden katılaşan döküme uygulanmasına bağlı olarak başlıca iki temel gruba ayrılabilir.
Doğrudan sıkıştırılmış döküm de kendi içinde, ıstampa hareketi ile başlatılan sıvı metal yer değişikliğine bağlı olarak ilave iki forma ayrılabilir; metal hareketi olmaksızın ve metal hareketi ile doğrudan sıkıştırılmış döküm. Metal hareketinin olmadığı birinci form özellikle ingot tipi parçalar için uygun iken, aynı zamanda geriye doğru işlem olarak da bilinen metal hareketini içeren ikinci form, daha kullanışlıdır ve şekil verilmiş parçaların yaygın olarak dökümleri için elverişlidir.
İlk olarak geliştirilen doğrudan sıkıştırılmış döküm, pistonlar, mastarlar ve ana silindirler gibi basit ve simetrik dökümleri üretmek için kullanılır. Doğrudan sıkıştırılmış dökümün kullanımı işlemin ve kalıp tasarımının özelliklerine bağlı olarak çok sınırlıdır: maksimum döküm ağırlığı genellikle 10 kg' dan fazla olamamaktadır. Metal hareketi ile doğrudan sıkıştırılmış döküm, otomobil endüstrisi için alaşım jantlar gibi karışık olarak şekillendirilmiş dökümlerin üretimini kolaylaştırdığından endüstriyel gereksinimler için daha uygundur.
Doğrudan sıkıştırılmış döküm düzenekleri basit ve açıktır. Dolaylı sıkıştırılmış döküm düzenekleri genellikle şu kategorilere ayrılır:
(i) düşey kalıp kapanması ve sıvı metale kuvvet uygulanarak içeri atılması,
(ii) yatay kalıp kapanması ve sıvı metale kuvvet uygulanarak içeri atılması,
(iii) yatay kalıp kapanması ve düşey olarak sıvı metale kuvvet uygulanarak içeri atılması,
(iv) düşey kalıp kapanması ve yatay olarak sıvı metale kuvvet uygulanarak içeri atılması.
Dolaylı sıkıştırılmış döküm makinalarının gelişimi temel olarak sıkıştırılmış döküm işleminin uygulanmasını da geliştirmiştir. Pratik olarak iç hataların olmadığı alaşım jantları gibi karmaşık dökümlerin üretimine olanak sağlamaktadır. Kalıp kaplaması gerekli değildir ve 100 MPa' ın üzerinde bir metal basıncı katılaşma boyunca uygulanır. Maksimum döküm boyutu makina kapasitesi tarafından sınırlanır. Bununla birlikte, dolaylı sıkıştırılmış döküm işleminin sakıncası 4 mm' den daha az bir duvar kalınlığı ile ince kesitlerin dökümü için yeterli olmamaktadır. Bunun nedeni düşük doldurma hızları ve erimiş metalin hızla katılaşmasıdır. Bundan başka, dökümün dışarı çıkarılmasının zor olduğu döküm ürünlerinin şekil karmaşıklığı üzerinde bazı sınırlamalar vardır. Geleneksel kalıp döküme göre dolaylı sıkıştırılmış dökümün daha düşük kalıp sıcaklığı, ince tane yapılı daha fazla soğuma hızı saklar. Dolaylı sıkıştırılmış döküm ürünleri, tane yönlenmesi ile karakterize edilen dövme işleminden daha homojen yapıdadır.
Sıkıştırılmış döküm erimiş alaşımın preslenmesi olarak kabul edilse bile, aynı zamanda yarı kapların şekillendirilmesi için de kullanılabilir. Buna göre yeni bir sınıflandırma şu şekilde yapılabilir:
(i) kristalizasyonun başlamasından önce,
(ii) yan katı presleme olarak da tanımlanabilen kristalizasyonun başlamasından sonra, yapılan sıkıştırılmış döküm.
Döküm Kalitesini Etkileyen Faktörler
Önem sırasına göre döküm kalitesini etkileyen faktörler şunlardır:
Alaşım
Döküm kalitesini etkileyen en önemli faktör alaşımın kendisidir. Alaşımın kompozisyonu ve erime sıcaklığı, ısıl iletkenliği, ısı transfer katsayısı ve kalıp malzemesi üzerine yapışması gibi fiziksel özellikleri kalıp ömrü üzerine doğrudan etkilerinden dolayı son derece önemlidir. Daha önemlisi, alaşımın cinsi döküm parametrelerinin, örneğin kalıp ömrü üzerine doğrudan etkisi olan kalıp sıcaklığının belirlenmesinde esas teşkil ederler. Bu nedenle sıkıştırılmış döküm genellikle alüminyum ve magnezyumun düşük erime sıcaklığına sahip olan alaşımları için kullanılmaktadır.
Eriyik Kalitesi ve Miktarı
Oksit miktarına bağlı olarak eriyik kalitesi sıkıştırılmış dökümde diğer döküm yöntemlerinden daha fazla önem taşır. Bunun nedeni, metalin dökülmesi sırasında kalıbın içinde kalan cürufları gidermek için gerekli olan yolluk ve girişlerin bulunmamasıdır. Hem demir hem de demir dışı alaşımları için oksit seviyesi, cüruf oluşturma, sıyırma ve/veya filtreleme işlemlerinin bir kombinasyonu ile yapılabildiği kadar en aza indirilmelidir.
Diğer taraftan, sıkıştırılmış dökümde absorblanan gaz döküm kalitesi için daha az öneme sahiptir. Çünkü uygulanan basınç seviyesi gazların hem oluşumu hem de eriyik içinde tutulmasını önlemek için yeterince yüksek seçilir. Bunun yanında, gaz absorbsiyonu eriyik sıcaklığının uygulanabildiği kadar en alt seviyede tutulması ile en aza indirilebilir. Uzun gaz giderme işlemleri gereksizdir, çünkü gaz boşlukları yeterli basınçla kolaylıkla giderilir. Gaz giderme işlemi genelde yalnızca ince kesitlerin varlığının yüksek döküm sıcaklığını zorunlu hale getirdiği ve aşırı gaz girişinin söz konusu olduğu durumlarda gereklidir.
Eriyik miktarı, net şekillerle çalışıldığı durumlarda önemlidir. Son ölçülerin kontrolü, döküm ağırlığı veya hacmi ölçülerek yapılabilir. Eriyiğin genelde yalnızca geniş çaplı hafif ağırlıklı parçalar için uygulanır. Geçerli olan yöntem, aşırı metal dökmek ve aşırı metali ya kalıbın dışına ya da dökümün kritik olmayan bir bölgesine uzaklaştırmak ve sonradan temizlemektir.
Düzenek
Sıkıştırılmış dökümün düzeneği dövme işleminde, kalıp dökümde veya kalıcı kalıp dökümde kullanılanlardan daha basit yapıdadır. Bu nedenle madeni eşya gereksinimi diğer yöntemlere göre daha azdır. Sıkıştırılmış döküm düzeneğinin başlıca elemanları; ıstampa (erkek parça), kalıp, dökümü dışarı çıkaran mil ve kalıbı ön ısıtmaya yarayan ısıtıcıdır. Ekipman, kullanım için bir hidrolik prese monte edilir. Bu hidrolik pres, parça geometrisine ve basınç ihtiyacına bağlı olarak tek etkili veya çift etkili olabilmektedir.
Sıkıştırılmış döküm kalıpları sürekli olarak terimi yorulma, çatlama, erezyon, korozyon ve çentik etkisine sebep olabilen termal ve mekanik çevrim yüklemelerine maruzdur. Bu nedenle kalıbın malzemesi, tasarımı, üretim yöntemi, uygun ısıl işlemi ve bakımı çok önemlidir. Kalıp malzemesi yüksek sıcaklıkta iyi sertliğe, yüksek temper direncine, yeterli tokluğa, özellikle yüksek derecede temizliğe ve düzenli mikroyapıya sahip olmalıdır. Alüminyum alaşımlarının ve daha birçok demir dışı alaşımların sıkıştırılmış dökümleri için kalıp malzemesi olarak genellikle H13 (ASTM 2344) ticari krom-molibdenli sıcak iş kalıp çeliği kullanılır. Demir esaslı malzemelerin uygulamalarında H13 kalıp çeliği temel olarak küçük büyüklükteki deneysel işler için kullanılabilir, çünkü H13 ile yapılmış kalıbın ömrü bu uygulamalar için sınırlıdır. Sonuç olarak yüksek sıcaklıkta erimiş çelikle temas eden kalıbın tungsten bazlı veya molibden bazlı malzemeleri içermesi gerekir.
Düzeneğin, erkek detaylarındaki köşe radyüsleri genellikle demir dışı malzemelerde 2 mm ve demir alaşımlarında 3 mm seçilir. Dökümü çıkartmayı kolaylaştırmak için çekme açılan kalıbın dış duvarlarından 0.5° ve ıstampa yüzeyinden ve katılaşmadan sonraki daralmaya bağlı olarak kalıp detaylarından 1-2° açıyla seçilir. Çekme açılarının uygun seçimi aynı zamanda uygulanan minimum basınç ile gözenekliliği azaltmak için gerekli uygun katılaşma modeli sağlayabilir.
Döküm Sıcaklığı
Kalıp boşluğu içine erimiş metalin döküldüğü sıcaklık hem döküm kalitesi hem de kalıp ömrü açısından son derece önemlidir. Çok düşük döküm sıcaklığı kalıbın doldurulması sırasında yetersiz akışkanlığa neden olur. Bunun sonucunda kalıbın doldurulması tamamlanamaz ve döküm yüzeyinde soğuk katlama hataları oluşur. Diğer taraftan, çok yüksek döküm sıcaklığı, sıvı metalin düzeneğin ara yüzeylerinin içine doğru ekstrüzyonuna sebep olabilir, aynı zamanda sıkıştırılmış dökümün kalın kesitlerinde büzülme gözenekliğine sebep olabilir. Tüm bunların yanında kalıp ömrü de yüksek döküm sıcaklığından etkilenir.
İdeal döküm sıcaklığı, alaşımın liküdüs sıcaklığı ve donma aralığının (liküdüs ile solidüs arasındaki fark) her ikisine birden bağlıdır. Genel olarak, liküdüsün üzerinde gerekli olan aşın ısıtma dar bir donma aralığı sergileyen alaşımlar için daha yüksektir. Bu tür alaşımlar kalıp duvarları üzerinde kabuk oluşumuna çok fazla eğilimlidir ve düşük iç kalite ile yüzey süreksizlikleri tarafından eşlik edilirler. Alüminyum alaşımları için, döküm sıcaklığı genellikle, liküdüs sıcaklığının 10-100 °C üzerinde seçilir. Alt limit, 7075 ve A390 alüminyum alaşımları gibi geniş donma aralığına sahip alaşımlarda uygulanabilir. Üst limit, dar donma aralığına sahip 3003 ve A413 alüminyum alaşımlarına uygulanabilir. İnce kesitli parçalar ve düzensiz profiller aynı zamanda, kalıbın doldurulmasını artırmak için daha yüksek döküm sıcaklığını gerektirmektedir. Bakır bazlı alaşımlar ve çelikler için, gerekli aşırı ısıtma, genellikle 30-150 °C arasındadır. Çünkü bu alaşımlar, metal kalıp ile temasta çok hızlı bir şekilde katılaşmaktadır.
Düzenek Sıcaklığı
Kalıp boşluğu ve ıstampa sıcaklıkları 200-300 °C arasında tutulur. 150 °C'nin altındaki düşük sıcaklıklar, kalıplarda termal yorulma hatalarını ve aynı zamanda döküm yüzeyi üzerinde soğuk katlanmaları başlatır. 400 °C'nin üzerindeki çok yüksek düzenek sıcaklıkları, sıcak noktalardan ve döküm içinde büzülme gözeneklerine sebep olabilir. Temel olarak demir bazlı alaşımların sıkıştırılmış dökümü için kalıbın aşırı ısıtılması ile ortaya çıkan diğer bir sorun ise, döküm ve kalıp arasında büyük bir kaynaklanma eğiliminin oluşumudur. Üretim şartları altında, birbirini izleyen dökümler arasında kalıplardan ısı çıkışı için kalıp malzemesinin çevresi yeterli olmalıdır ve gerekli yerlerde seçilen su soğutması veya buhar soğutması ile arttırılmalıdır.
Basınç Uygulamasından Önceki Bekleme Zamanı
Optimum sonuçlar basıncın erimiş metale sıfır akışkanlık sıcaklığının yakınında uygulandığı zaman bulunur. Sıfır akışkanlık sıcaklığı sıvı metalin akış özelliklerini kaybettiği sıcaklığın altındaki sıcaklık olarak tanımlanır. Bu sıcaklık genellikle, alaşımın solidüs ve liküdüs sıcaklıkları arasındaki mesafenin orta noktasıdır. Bununla birlikte, ergimiş metalin liküdüs sıcaklığında veya altında kalıp içine dökülmesi kullanışlı değildir. Netice olarak, daha önce tanımlandığı gibi, eriyik aşırı ısıtılmış şartlarda dökülür ve liküdüs sıcaklığının altına soğumasına izin verildikten sonra basınç uygulanır. Alüminyum alaşımlarında, kalıp kapanması ve basınç uygulanmasından önce 10-20 saniye arasında bekleme sağlamak çoğunlukla yeterli olmaktadır.
Bununla birlikte, çelik döküm durumlarında metal optimum presleme sıcaklığına kalıpla ergimiş metal arasındaki yüksek sıcaklık farkı sebebiyle çok hızlı bir şekilde ulaşır. Planlanmış bir bekleme, 60 mm kalınlığın üzerindeki kalın kesitli döküm durumlarının dışında nadiren gereklidir.
Yağlama
Isı transferi ve katılaşma hızını kontrol etmek için kullanılan ticari olarak ayine malzemeler, yarı sıvı metalin ters akışı ile basınç altındaki düzenekte kalıba belli orana kadar tutunabilmesinden sıkıştırılmış dökümde kullanılamazlar. Dökümler arasında sıcak kalıpların üzerine kollaidal grafitin ince bir tabaka oluşturacak şekilde püskürtülmesi, demir dışı ve dökme demir uygulamalarının birçoğu için tatmin edici sonuçlar vermektedir. Ticari grafit dövme yağlayıcıları genel olarak yeterlidir.
Çelik dökümleri için, ergimiş çelik ile temas eden kalıp yüzeylerine sıcakken ayırıcı etkiye sahip seramik yağlayıcılar püskürtülebilir. Bunlar, sıvı bir ortam içinde bir bağlayıcı ve alümina tozunun karışımı şeklinde ticari olarak kullanılmaktadır. Bu tabakanın kalıp yüzeyleri üzerindeki sürekliliği, sıkıştırılmış çelik döküm ile kalıp arasındaki difüzyonun azaltılmasında önemli bir etkendir.
Bütün uygulamalar için, kalıpların havada 350 °C' ye ısıtılarak ön işleme tabi tutulması istenir. Böylece aşınma ve kaynaklanmayı engelleyen koruyucu bir oksit tabakası oluşmaktadır.
Basınç Seviyesi ve Süresi
Demir ve demir dışı malzemelerin çoğunluğunda büzülme gözeneklerinin ve gaz boşluklarının oluşumunu engellemek için 70-105 MPa arasında bir basınç seviyesi yeterlidir. Bununla birlikte bazı durumlarda dökümün geometrisi, sık sık kalıbın doldurulması ve gözenek kontrolü için daha yüksek basınç kullanılmasını zorunlu kılmaktadır.
Dökümün katılaşan son parçası, genellikle gözeneklik olayının en hassas olduğu alandır. Gözenekliğin azaltılması, sıvı veya yarı-sıvı metalin katı yapı örgüsüyle "ayrılma-beslemesi" yapılmasıyla olur. Katı bölgeyi tamamıyla ayıran bu metal akışı olduğu zaman (genellikle en son katılaşan bölgenin hemen yakınında oluşur) katılaşan bölgedeki kabuğa basınç uygulamak için bu bölgede belli bir plastik deformasyon olmak zorundadır. Dökümün en son katılaşan parçasında 70 MPa' lık bir basınç seviyesine erişmek için gerekli, pres kuvvetinin dökümün kesit alanına bölünmesi ile tanımlanan nominal basınç, sıkıştırılmış dökümün geometrisine bağlı olarak bu seviyede iki kere oluşmalıdır.
Kusursuz döküm sağlayan minimum basınç seviyesinin üzerinde artan basınç seviyesinin, küçük ek yararlar sağladığı bulunmuştur. Aynı zamanda dökümün akma dayanımını aşan çok yüksek basınçların tane incelmesi ve daha yüksek özellikler sağladığı bilinmektedir. Bu ek yararlar, daha yüksek pres kapasitesi gereksinimi ile yüksek basınç ve yüksek sıcaklığın kombinasyonuna bağlı olarak ortaya çıkan artan maliyetlerle karşılaştırılmalıdır. Bununla birlikte, sıkıştırılmış döküm içerisindeki büzülme ve gaz boşluklarının tüm eğilimlerini ortadan kaldırmak için yeterli bir çevre basıncından yararlandır. Bu basınç, genellikle basit şekiller için 70-105 MPa arasında olan basınç seviyesinde, ince ve karmaşık şekillerde ise 140-210 MPa arasındadır.
Dökümün şekli ve kesit kalınlığı, sıkıştırma basıncı altında katılaşmanın tamamlanmasını sağlamak için gerekli basınç süresini belirlemektedir. Minimum gerekli sürenin ötesinde, daha uzun bekleme süresi küçük yararlar sağlar ve aslında duvar çatlamalarına ve rijit ıstampa üzerindeki dökümün termal daralmasına bağlı olarak ıstampanın geri çekilmesinin zorlaşmasına sebep olabilir.
Sıkıştırılmış Dökümün Üstünlükleri ve Sakıncaları
Sıkıştırılmış döküm tekniği geleneksel döküm yöntemleri ve deformasyon işlemleri üzerine başlıca şu üstünlüklere sahiptir:
1. Daha yüksek mekanik özellikler. Akma dayanımları %10-15 ve yüzde uzamaları ile yorulma dayanımları %50-80' e kadar arttırılır.
2. Yüksek sıcaklıklarda ısısal kararlılık.
3. Daha ince mikroyapı.
4. Geleneksel döküm işlemlerine göre segregasyonun en aza indirilmesi, porozitenin engellenmesi.
5. Net veya net şekle yakın üretim sağlaması ile karmaşık şekillerin ve ince detayların üretilmesi (net şekil kapasitesi). 100 mm' de 0.25 mm — 500 mm' de 0.6 mm ölçüsel doğruluk sağlaması.
6. Isıl işlem görebilme.
7. Kaynaklanabilme kabiliyeti.
8. Kusursuz yüzey bitirme.
9. Yüksek verimlilik. Dövmenin tersine daha az enerji gereksinimi, basit hareket işlemiyle üretim sağlaması ve geri dönüş için hemen hemen hiç hurda olmaması. Ayrıca döküm işlemine göre daha yüksek üretim hızı sağlaması.
10. Sıcak veya soğuk dövme işlemlerinden daha az basınç gereksinimi ile ekipman ve kalıp malzemesi ihtiyacının azaltılması. Herhangi bir besleme sistemi, yolluk, girişler, büzülme giderici birimler, besleyiciler olmadan tamamlanabilmesi.
11. Kompozit üretimine uygulanabilmesi ve özel alaşımların dökülebilmesi. Demir dışı ve demir alaşım kompozisyonlarının bir çok çeşidinin (hem döküm hem de dövme) kullanılmasına imkan vermesi.
Sıkıştırılmış dökümün sakıncaları şu şekilde sıralanabilir:
1. Yüksek maliyet (başlıca hidrolik pres ve kalıbın ön ısıtılması için gerekli ısıtıcı sistem).
2. Kalıp ömrünün kısalması.
3. Karmaşık şekilli parçaların üretiminin sınırlanması.
4. İnce kesitlerin üretim zorluğu.
5. Sınırlanmış maksimum boyut ve ağırlık. Çubuk, boru ve plaka üretimi için uygun değildir.
6. Kalıp boşluğu içinde türbülanslı akışa bağlı olarak ortaya çıkan kusurlar.
7. Katılaşma sırasında oluşan dentritik yapıya bağlı olarak homojen olmayan mekanik özellikler.