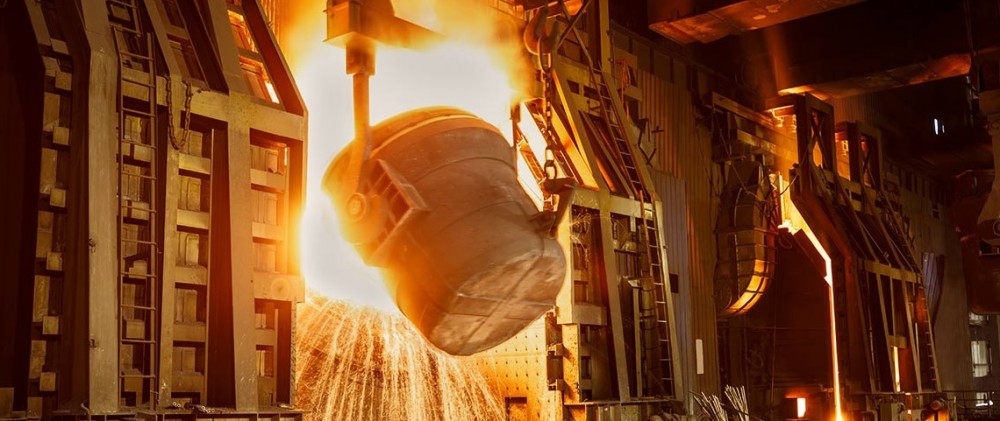
Sıvı çeliğin, direkt redüksiyon ve oksijen üflemeli konverterlerin kullanılmasıyla üretimi bugün çok yüksek bir düzeye ulaşmıştır. Buna paralel olarak sıvı çeliğin kütük, blum, platin veya H, I profilleri gibi daha kolay ve seri halde biçimlendiremeye yarayan sürekli döküm yöntemleri geliştirilmiştir. Bu sayede eski klasik yönteme göre büyük ölçüde işlem sayısı azalmış, malzeme, enerji ve zaman tasarrufu sağlanmıştır.
Sürekli döküm yönteminde insan gücü ihtiyacı azaldığı gibi çalışma şartlarıda çok iyileştirilmiştir. Halen gelişme halinde olan bu yöntemin en üstün yönlerinden biri döküm veriminin çok yüksek olmasıdır. Bilindiği gibi blok dökümünde ingotlarda katılaşma esnasında kof bölge oluşmaktadır. Merdanelere temas ettikten sonra parçalardaki bu boşluklu kısımların kesilmesi gerekmektedir. Sürekli dökümde ise söz konusu blok, sürekli olarak döküldüğünden katılaşma da bloğun bir tarafından sürekli devam etmekte dolayısıyla boşluk kayıpları ortadan kalkmaktadır. Böylece klasik ingot dökümüne göre verim sürekli döküm yönteminde %95’in üzerinde çıkmaktadır.
Bugün artık sıvı çeliğin genel anlamda biçimlendirilmesi sürekli döküm yöntemi sayesinde her kapasitedeki çelik dökümhanesinde mümkün hale gelmiştir. Bu yöntemin esasını, iki tarafı açık, su ile soğutmalı, istenen profil kesitli bir kalıp ile bu kalıptan kısmen katılaşmış iş parçasını sürekli çekmeye yarayan merdaneler oluşturur. Kalıbı sürekli, sıvı metalle besleyen bir ara pota (dağıtıcı, tandiş) soğutma, su püskürme donanımı ve kesme mekanizması sistemi tamamlayan elemanladır.
Sürekli döküm donatımları genellikle yatay ve düşey olmak üzere iki tarzda kurulurlar. Yatay döküm tarzının düşey döküm tarzlarına göre birçok üstün yönleri vardır. Bu nedenle döküm malzemesi imkân verdiği ölçüde donatım yatay döküm donatımı olarak kurulur. Demir olmayan metallerin tümünü yatay döküm tezgâhlarında dökmek mümkündür. Ancak çeliğin yatay sürekli dökümünde bazı güçlükler mevcuttur. Bu güçlüklerin en önemlisi dağıtıcı kalıba bağlayan geçiş kısmından kaynaklanmaktadır. Çeliğin döküm sıcaklığı, yüksek olduğundan bu sıcaklığa dayanan, az aşınan, kolay bağlanabilen, uzun ömürlü geçiş kısmına ihtiyaç vardır. Bu özelliklere sahip bir geçiş kısmı geliştirilinceye kadar çeliğin sürekli dökümü düşey donatımlar yardımıyla yapılmıştır.
Önerilen Makale: Çelik profil ve uygulamaları hakkında detaylı bilgi almak için
çelik profil çeşitleri sayfamızı ziyaret etmenizi tavsiye ederiz.
Düşey Sürekli Döküm Yöntemi
Düşey döküm işlemi şu an mevcutta kullanılan, en çok tercih edilen yöntemdir. Sistem aşağıda gösterilen sıra ile iyileştirmelere uğramış ve son halini almıştır. Temel olarak prensibini anlatmak gerekir ise; döküme başlarken önce sıvı metal potadan dağıtıcıya alınır. Dağıtıcıdan kalıba sıvı metal akışı metalin potadan dağıtıcıya geçişini el ile veya otomatik olarak ayarlayarak sağlanır. Kalıptan çıkarken kısmen katılaşmış olan döküm, merdaneler ile düşey olarak aşağıya doğru çekilir. Kalıptan çıktıktan sonra üzerine su püskürtülerek hızla katılaşması sağlanır. Sürekli bir çubuk olarak aşağıya doğru ilerleyen döküm alt ucundan belirli bir uzunlukta kesilerek parçalar halinde uzaklaştırılır.
Döküm sıcaklığı, normal döküm işleminde olduğu gibi sürekli dökümde de hatasız ve arızasız bir döküm için malzeme çeşidine bağlı olarak en uygun döküm sıcaklığının saptanması ve sağlanması gereklidir. Bu sıcaklığın saptanmasında dökülen çelik türünden başka pota hacmi, pota taşıma ve boşaltma süresi önemli faktörlerdir. Döküm parçasının kalıptan çıktıktan sonra eşit soğuma şartlarında daha kısa mesafede katılaşması istenir. Bu ise döküm sıcaklığının mümkün olduğu kadar düşük tutulması ile sağlanır. Ancak döküm sıcaklığının belirli bir değerin altına düşürülmesi erken katılaşarak memeleri tıkama, akışın kötüleşmesi gibi sorunlara yol açabilir.
Döküm süresi kısaltılabildiği oranda aşırı ısıtma sıcaklığı da düşürülebilir. Böylece enerjiden ve refrakter malzemeden tasarruf sağlamak da mümkün olur.
Eğmeli düşey sürekli döküm, çember kavisli sürekli döküm, oval kavisli sürekli döküm tarzları da ayrıca sanayide kullanılan yöntemlerdir. Eğmeli sistemde eğme doğrultma makaralı sistemi aşağıya kadar düşey olarak ilerleyen döküm parçası çekme makaralarını geçtikten sonra eğme makaraları yardımı ile bükülerek yatay konuma geçirilir.
Böylece istenen uzunlukta parça dökülebilir. Parça eğme bölgesine geldiğinde tamamen veya hemen hemen katılaşmış durumdadır.
Çember kavisli döküm tarzında ise yapı yüksekliği %50 oranında azaltmış, çekme ve doğrultma işlemlerinin tek bir merdane grubunun yapması sağlanmıştır. Kalıp kavisli olarak imal edilerek, döküm boruları kullanılmakta veya düz imal edilerek kavisli döküm yolu kullanılmaktadır.
Oval kavisli yöntemde ise, kalıp kavisli imal edilerek sıvı metalin kalıba giriş asimetriktir. Merdaneler yardımıyla doğrultulan ve çekilen parçanın yatay olarak bükülmesi yapılır.
Sürekli döküm tesisatının ana yapı elamanları şunlardır;
1. Pota
2. Dağıtıcı pota (tandiş)
3. Döküm kalıbı
4. İlk hareket başlığı
5. Çekme ve doğrultma merdaneleri
6. Kesme donatımları
7. Soğutucu ızgaralar
8. Karıştırma donatımları
9. Soğutma donatımları
10. Ölçme ve kontrol donatımları
Avantajları
1. Sıvı metal kalıba tamamen simetrik olarak girer ve katılaşır
2. Düz kalıbın imalatı kolaydır.
3. Basit, düz bir çekme başlığı kullanılır.
Dezavantajları
1. 30 metreyi aşan yapı yüksekliği ile tesis masrafını çok arttırır
2. Döküm parçalarının maksimum yüksekliği bina yüksekliği ile sınırlıdır.
3. Kesme donatımındaki kısa süreli bir arızada bile döküm işlemi durur.
4. Kesilen parçaları yana yatırmak için bir donatıma ihtiyaç vardır.
5. Döküm esnasında pota zeminden çok yüksekte bulunur.
Yatay Sürekli Döküm Yöntemi
Metallerin sürekli dökümünde döküm kalıbı bütün gelişim evrelerinde düşey olarak düşünülmüştür. Bunun teknik ve ekonomik açıdan olumsuz yönleri vardır. Yatay sürekli döküm yönteminde kalıp yatay durumdadır. Konveksiyonel yöntemdeki gibi kalıp ile tandiş bağlantısı arasında boşluk olmaktadır. Buda yatay süreki döküm işlemine bazı avantajlar sağlamaktadır. Özellikle Tandiş ile kalıp arasındaki metal oksidasyonu ortadan kalkmakta, tandişten kalıba metal akışının kontrolünün yapılmasına gerek kalmamakta ve tandişten kalıba kaçan parçacıkların yavaş akış dolayısı ile azalması örnek olarak verilebilir. Bu yöntemde kullanılan kalıplar yüksek oranda sertleştirilmiş, alaşımlandırılmış ve ısısal direnç kazandırılmış bakırdan imal edilmektedir. Kalıplar su soğutma donatımları ile çevrelenmiştir. Yatay sürekli dökümde bu zamana kadarki gelişmeler daha çok döküm hızının ve parça kesitinin arttırılması yönünde olmuştur. Isı iletimi, difüzyon, dayanım ve ekonomik şartlar gelişmeyi sınırlayan başlıca faktörlerdir. Dağıtıcı pota ile kalıbı bağlayan seramik geçiş kısmının dayanımını arttırmak, parça yüzey hatalarını azaltmak için kalıptan çekme mekanizmalarını geliştirmek için çalışmalar sürmektedir.
Yatay sürekli döküm sistemleri için geliştirilmiş birkaç farklı yöntem vardır. Bunlar; General Motor firmasının geliştirdiği iki parçalı kalıplı sistemler, Davy-Loewy in geliştirdiği 75-150 mm çapında veya eninde kare kesitlerin dökülebildiği sistem, Horicast denilen katılaşma bantlarının kullanıldığı sistem, Böhler yöntemi ise kalıp içerisinde mümkün olduğu kadar çabuk bir hidrostatik basınç oluşturmak için dağıtıcı tabanı çıkış ağzına doğru daralmaktadır. Tulachermet sistemi ise Rusyada geliştiren bir sistemdir ve bu yöntem ile 60-150mm çaplı veya 80-120mm kare kesikti paslanmaz çelik kütükler dökülebilmektedir. IRSID sistemi ise Fransada geliştirilmiş ve geçiş kısmındaki sıvı metalin havadan gaz emmesini önlemek için bu bölgeye koruyucu asal gazlar gönderilir. Technikon sisteminde ise kalıp direk olarak dağıtıcıya bağlı değildir ve bir araba üzerinde bulunmaktadır. Kalıp dolduktan ve katılaştıktan sonra, araba ile beraber, belirli bir hızda çekilir. Stewarts-Llayds sisteminde ise yatay konumdaki kalıp dirsek şeklinde bir geçiş kısmı ile bir basınçlı pota altına bağlanarak, sıvı metal üzerine pülzasyon şeklinde yapılan basınç ile döküm parçasının ilerlemesi sağlanır. Bunlar dışında Concast firmasının geliştirdiği osilasyon hareketi yapan yatay kalıba dağıtıcı potadan sıvı metal elektromanyetik kuvvetlerle bağlantı yapılmadan sağlanmaktadır. Diğer bir firma Voest ise yatay silindirik kokili ekseni etrafında osilasyon hareketi ile döndürerek daha düzgün bir yüzey kalitesi sağlamıştır. Burada dönen kalıpla geçiş bileziği arasındaki sızdırma, ikisi arasında preslenen bir yağlama ise önlenir.
Avantajları
1. Tesisatın yüksekliği çok az olması nedeniyle mevcut herhangi bir çatı altına kurulabilir. Böylece ilk tesis masrafları %30 oranında düşer.
2. Tandiş ile kalıp birbirine bağlı bir birim oluşturduğundan, normal yöntemlerdeki sıvı metalin ara potadan kalıba geçişteki oksidasyon tehlikesi ve önlemleri söz konusu değildir. Bu yöntem parça boyutları 100 mm ‘den küçük yuvarlak ve kütük dökümünde büyük avantaj sağlar.
3. Sürekli döküm parçasını eğme ve yöneltme zorunluğu olmadığından düşey olmadığından, düşey yöntemde kalite sorunları yaratan alaşımlar bu yöntemde dökülebilir.
4. Hiçbir döküm yardımcı malzemesi kullanılmadığından, düşey sürekli döküme göre ısı iletimi daha büyüktür.
5. Tesisatın yüksekliğinin çok az olması, kullanma ve bakım işlemlerini kolaylaştırır. Pota-dağıtıcı-kalıp sistemi otomasyonla kontrole çok müsaittir. Böylece personele olan bağımlılık ortadan kalkar.
6. İlk tesis masraflarının %30 kadar daha düşük olması, küçük siparişli parçalarında bu yöntem ile ekonomik olarak üretilebilmesini sağlar.
Sürekli Döküm Yöntemi Donatım ve Teçhizatları
Kalıp sürekli döküm sürecinin en önemli parçasıdır. Burada başlayacak bir hata sürekli döküm mekanizmasının diğer kısımlarına doğru giderek artmaktadır. Kalıbın ana görevi sürekli dökümde, dökülmekte olan metale şekil vermesidir. Bu şekil verme işlemi yüksek sıcaktaki sıvı çeliğin kalıbın cidarları tarafından soğutulmasıyla olmaktadır.
Kalıp yüksekliği 500–1500 mm arasındadır, bu yükseklik üretilecek ürüne göre değişmektedir. Slab için 1200 mm civarındadır. Blum için daha küçük boyutta olabilir. Kalıbın çalışma bölgesinin, yani sıvı çelikle temas eden bölgesinin (bakır cidarın) ısı geçirgenliği mümkün olduğu kadar yüksek olmalı aynı zamanda yüksek mekanik özelliklere sahip olmalıdır. Soğutma suyu kalıba alttan girip üstten çıkmaktadır. Dolaşım sırasında su 4°C–12°C ısınır, dolaşım hızı 6000–10000 mm/sn’dir. (15°C–20°C) Daha sıcak ve daha düşük hızla dolaşır ise soğutmayı iyi sağlayamadığı gibi su içindeki kireç vb. empirüteler kanalları daha kısa zamanda tıkarlar.
Kalıptan geçen çelik, kalıbın hemen bitiminde 20-30 mm’lik katılaşmış bir kabuğa sahip olmalıdır. Bu onun kalıptan sonra gelen işlemlerde deformasyonlara uğramaması için yani külçenin içindeki sıvı faz ile sürekli döküm makinesinin mekanik teçhizatına ait basınçlara dayanabilmesi için gereklidir. Bundan dolayı kalıpların yüksekliklerini tespit ederken külçenin kalıp bitiminde belli bir kabuk kalınlığına sahip olması esas göz önüne alınmalıdır. Ayrıca belirli bir kabuk oluşması ile malzeme kendini çekerek çıkışa doğru profil boyutları küçülür ve parçanın kalıp iç yüzeyleri ile teması kesilir. Bunun sonucu ise daha yavaş katılaşması ve soğuması, daha ince bir kabuk oluşmasıdır. Bunu önlemek için kalıbın kesiti çıkış yönüne doğru döküm metalin kendine çekme özelliğine göre konikleştirilir. Böylece döküm parçasının kalıptan çıkıncaya kadar kalıp yüzeyi ile sürekli temas sağlanır.
Kalıptan kesitinin çıkış yönündeki bu kesit daralmasına kalıbın konikliği denir. Döküm malzeme türünden başka, döküm hızı, döküm sıcaklığı (aşırı ısıtma) verilecek koniliği belirleyen önemli faktörlerdir.
Pratik tecrübelere göre daire kesitli kalıplarda koniklik %0,4–0,9 mm arasında değişmektedir. Prizmatik kesitli kokillerde dar kenarlara aşağıya doğru %0,9–1,3 mm arasında verilen bir koniklik yeterli olmaktadır. Geniş kenarlar sıvı metalin hidrostatik basıncı ile kalıp yüzeyine bastırılabildiğinden bu kenarlara koniklik verilmez.
Döküm parçasının kalıptan çıktığı andaki katılaşmış cidar kalınlığı iç kısımdaki halen sıvı halde bulunan sıvı metal üzerine gelen hidrostatik basıncı taşıyacak dayanımda olması gerekir. Bu katılaşan kabuk kalınlığı ile döküm hızına, malzeme özelliklerine ve soğuma şartları ile kalıp kesit boyutları ve şekli gibi birçok faktöre bağlıdır.
Kalıpta yapılan işlemler aşağıdaki gibidir.
Kalıp önce kalıp yağı ile yağlanır. Bu yağlamanın amacı yapışmanın önlenmesidir. Kukla kafası kalıp içine belli bir miktar girdikten sonra, kalıp ile arasında kalan boşluk asbest iple kapatılır. Kalıba gelen ilk çelik kukla kafasına çarpıp orda katılaşır. Burada ilk katılaşmayı sağlamak amacıyla çelik talaşı ve çelik bilyalar konur. Döküm başlayınca, kukla kafası katılaşan çeliği döküm hızıyla aşağı doğru çeker. Kalıpta yapışmayı önlemek için devamlı yukarı aşağı osilasyon hareketi vardır. Döküm sırasında kalıba devamlı döküm tozu atılır. Bunun amacı kalıptaki sıvı çeliğin oksitlenmesini önlemek, ısı kaybının önlemek, çelik ile kalıp arasında yağlama yapmak ve çelikteki pislikleri alıp çelik yüzeyine vererek ince bir cüruf tabakası oluşturmaktır. Yağlama işlemi bilhassa yüksek sıcaklıktaki çelik dökümlerinde büyük önem kazanır. Yeterli derecede yağlama yapılmazsa sıvı çeliğin kalıp yüzeyine yapışması bu çeşit çelik dökümünde daha kolaydır. Yağlamada kullanılan malzemeler bir takım özelliklere sahip olmalıdır. Sıvı ve katı olarak iki çeşit yağlayıcı malzemeler kullanır. Bunlar doğal, madeni, parafin, kauçuk ve grafit olabilir. Kalıplar sürekli dökümde üç tip olarak kullanılmaktadır;
1. İnce cidarlı yekpare çekme kalıplar
2. Plaka kalıplar
3. Dövme blok tipi kalıp
Bu kalıpların tümü dörter cidardan oluşmaktadır. Cidarlar dökülecek malzemenin cinsine göre boyut alırlar. Isı iletkenliğinin yüksek oluşu nedeniyle sürekli döküm tesislerinde su soğutmalı kalıp malzemesi olarak bakır seçilmektedir. Isıl iletkenliğinin biraz daha az olmasına karşın ömürlerinin daha uzun olması nedeniyle Cu-Ag, Cu-Cr, Cu-Zr gibi alaşım elementleride kullanılırlar. Örneğin %0.5–0.3 Cr alaşımlı bakır kalıpların sertliği 130 HB’dir. Sert Cr kaplamayla kalıp iç yüzeylerinin sürtünme katsayısı düşürülerek ve daha dayanıklı 230-250 HN Cu kalıp tipleri geliştirilmiştir. Kaplanan Cr tabakasının kalınlığı 0.07mm olması yeterlidir. Bunların dışında iç yüzü Mo püskürtülerek kaplanmış kalıp türleride vardır.
Döküm Potası
Sürekli dökümde kullanılan potalar sürekli akışlı potalardır. Çünkü devirmeli potalarda, sıvı metal banyosunda istenmeyen çalkantılara ve metalin havadan gaz emişine böylece oksidasyonuna sebeb olurlar. Sıvı metal pota tabanından alınması için tabanda bir delik bulunur. Bu delik tıkaçlı veya sürgülü olarak açılıp kapanabilir. Metalin delikten akış debisi ayarlanabilir. Potada sıcaklık ayarı önemlidir. Ocaktan veya konvertörden gelmiş olan sıvı metalin tandişe geçmeden önceki sıcaklığı çok önemlidir. Sorunsuz uygun bir katılaşma için bu sıcaklık dökülecek olan malzeme için ısı kaçışları dikkate alınarak hesaplanmalıdır.
Tandiş
Kalıp ve Pota arasında kalan bu elemanın görevi, sıvı metali depo ederek bir veya birkaç kalıba istenilen şekilde dağıtmaktır. Kalıpların belirli bir basınç ve debide kesintisiz beslenmesi gerektiğinden, bu işi sıvı metali bir yerden bir yere taşımaya yarayan potalarla yapmak mümkün değildir. Boyutları kalıpların döküm kapasitelerinin toplamına göre saptanır. Önemli olan nokta sıvı metalin dağıtıcı içinde mümkün olduğu kadar homojen bir sıcaklıkta ve en az kayıpla tutulmasıdır. Bu amaçla içine refrakter tuğla ve ısı yalıtım elemanları bulunmaktadır. Eskiden ısı kayıplarını engellemek zor olduğundan, bürlörler ile ısıtarak bu ısı kayıpları telafi edilmekteydi. Günümüzde yalıtım teknolojisi çok geliştiğinden gerek kalmamıştır.
Daldırılmış Döküm Borusu
Slab veya büyük kesitli dökümlerde sıvı metal, dağıtıcıdan kalıba bir boru içinden geçerek dolar. Sürgülü ve tıkaçlı dağıtıcılar kullanıldığı zaman, sıvı metalin kalıba geçişi bu boru ile olmaktadır. Bu borunun başlıca yararları, serbest düşüm ile kalıp banyosu arasındaki örtü, cüruf parçalanmaz, kalıbın türbülanssız dolması sağlanır, Sıvı metal demetinin akarken havadan gaz emmesi, okside olması ve soğuması önlenir. Bunun sonucunda sorunsuz bir döküm işlemi ve daha kaliteli parça üretimi mümkün olur. Boru genelikle belirli bir derinliğe kadar metal banyosu içine daldırılır. Borunun alt ucu çok kere kapalı olup, metal çıkışı yanlardan ve muhtelif açılarda olmaktadır. Döküm boruları zirkonsilikat (ZrSiO4) ve zirkonoksitten tek parça halinde imal edilirler.
Püskürtme Nozülleri
Soğutma suyu parça yüzeyine genellikle çeşitli meme biçimleri ile püskürtülerek gönderilir. Meme seçiminde; istenilen püskürtme tarzı, suyun parça yüzeyine çarpma enerjisi gibi faktörler rol oynar. Püskürtülen su demeti geometrisi, dolu koni, içi boş koni veya yelpaze şeklinde olabilir. Buna göre dolu koni biçimindeki bir püskürtmenin parça yüzeyindeki izi daire, diğerlerinde ise sırasıyla halka ve kenarları birbirine paralel birer banttır.
Meme tipini seçerken, parça şekli ve kalitesi, döküm hızı, kılavuz merdanelerin konstrüksiyonu dikkate alınır. Örneğin ikinci soğutma bölgesinde kılavuz merdaneleri seyrek dizilmiş bir kütük döküm tesisatında dolu koni biçimi püskürtme kullanılır. Bu biçimdeki parça yüzeyine çarpan su demetinin şiddeti parça kenarlarında zayıf orta bölgede kuvvetlidir. Yelpaze biçimindeki püskürtme, merdaneleri kısa aralıklara düzenlenmiş bütün makine tiplerinde kullanılmaktadır.
İçi boş koni biçimindeki püskürtme köşeleri kuvvetli soğutulması istenen kütük dökümleri için kullanılmaktadır. Meme şekillerine bağlı püskürtme karakteristiklerinin sürekli dökümde değişen imalat programına göre kolayca seçilebilmesi için meme donatımlarında da gelişmeler devam etmektedir.
Etkin bir soğutma için döküm parçası yüzeyine püskürtülen suyun her bir damlası parça yüzeyinde soğutmayı güçleştiren buhar tabakasını parçalayacak şiddette olması gerekir. Suyun içinde parça yüzeyine çarpan su damlacıklarının belirli bir kinetik enerjiye ulaşması icap eder. Bu kinetik enerji ile önündeki su basıncına ve damla büyüklüğüne göre değişir. Örneğin kütük dökümü için oval yelpaze biçimindeki püskürtmede çarpma basıncının yaklaşık olarak 0.08–0.17 p/mm2 civarında olduğu saptanmıştır.
Gereksiz su sarfiyatından kaçınmak için beher çift merdane başına nozül sayısı çok kere iki veya üç adetle sınırlandırılır. Yalnızca su püskürtme yerine son senelerde suyu basınçlı hava ile pülverize ederek püskürten nozüllerde geliştirilmiştir. Ancak burada havanın parça yüzeyinde oksidasyonu kolaylaştıracağını gözden uzak tutmamak gerekir. Isıl gerilmelere çok hassas olan çelikler su püskürtülmeden tamamen havada ışınım yoluyla soğutulurlar.
Destek Plakaları
Destek plakaları slab dökümlerinde kalıp çıkışında hem henüz ince bir kabuk tarafından taşınan parçayı desteklemek, hem de kalıpla püskürtme bölgesi arasında tedricî bir soğutma bölgesi sağlamak amacıyla kullanılırlar. Kalıptan sonra gelen bu plakalara soğutma plakalarıda denir. Plakalar genellikle bakır veya çelikten yapılmaktadır. Su ile soğutulurlar. Üzerlerinde ayrıca parçayı su ile direk olarak soğutmaya yarayan deliklerde bulunur. Plakaların kendilerini kolayca soğutabilmek için dış taraflarına soğutma kanatları yapılmıştır. Bu çeşit plakalar aşınmaya dayanıklı çelik veya hematitten dökülerek imal edilirler.
Plakalar parçanın karşılıklı iki geniş yüzeyine 1.5–2 mm aralıklarla kalıbın bir uzantısı şeklinde arka arkaya dizilmişlerdir. Kalıbı ilk takip eden plaka çifti kalıba bağlı olup onunla beraber bir osilasyon hareketi yapar. Bu tür soğutma tarzı başlangıçta yalnızca slab dökümü için uygulanmış olmak ile birlikte bugün diğer bazı dikdörtgen kesitli parçalarda da kullanılmaya başlanmıştır.
Destek plakaları ile soğutma direkt ve endirekt olarak iki şekilde meydana gelmektedir. Direkt soğutma plakalar üzerindeki deliklerden parçaya püskürtülen su ile endirekt soğutma ise plakaların parçaya teması ile sağlanmaktadır. Plaka üzerindeki püskürtme delikleri plakaları soğutan 1 atü basınçlı su devresine bağlıdır. Püskürtme suyu bu devreden deliklere geçer.
Bu soğutma sisteminde karşılıklı her bir plaka çifti parçaya basarak ve çekerek onunla birlikte belirli bir süre aşağıya doğru hareket ederler. Daha sonra parçadan ayrılarak hızla ilk konumuna gelir ve tekrar parçayı kavrarlar. Örneğin 25mm/sn (1,5m/dak) bir döküm hızında plakaların parçadan ayrılıp geri hareket süresi 0.8 saniyedir. Destek plakaları sayesinde özellikle slab dökümlerinde yüzey deformasyonları, çatlaklar ve iç gerilmeler azaltılmıştır.
Makine Soğutma Devresi
Birincil ve ikincil soğutma devreleri dışında döküm donatımı ve makinesine ait diğer elemanların (Çekme, destek, eğme, doğrultma merdaneleri, kesme istasyonu hidrolik devreler vs.) soğutulması devre içinde incelenir.
Yedek Soğutma Devresi
Bu devre elektrik kesintisi gibi acil durumlarda otomatik soğutma devresine bağlanır. Bu devreye basınçlı su, yükseğe yerleştirilmiş bir su deposu veya bir dizel motor-pompa sistemi ile temin edilir. Depo kullanıldığı takdirde, kalıbı en az 10 dakika sürekli soğutacak ve 2 atü’lük bir su basıncı sağlayacak yükseklikte olmalıdır.
Asal Gaz ve Üflenmesi
Potadaki sıvı metal içine aşağıdaki amaçlarla asal bir gaz, çoğunlukla Argon gazı, üflenir. Bu sayede sıvı metal içindeki deoksidasyon artıklarını temizlemek, sıvı metalin hidrojen miktarını azalmak, üflenen gazın karıştırma etkisi ile potada homojen bir sıcaklık dağılımı sağlanır. Potaya gaz iki yolla üflenir. Birincisi pota tabanına açılmış deliğe yerleştirilmiş gözenekli bir taş içinden, ikincisi potaya yukarıdan daldırılmış refrakter astarlı bir milin ortasındaki delikten üflenerek yapılır. 100 ton sıvı metal ihtiva eden bir pota için üfleme süresi 10 dakikadır. Üfleme işlemi, potada üfleme süresi ve debisine bağlı olarak yaklaşık olarak 1°C/dak’lık bir sıcaklık düşümüne sebeb olur. Argon gazının eklenmesi ile karıştırma işlemi arttırılmış olur, nozüllerde tıkanma tehlikesi azalır ve katın inklüzyon parçacıklarının ayrılmasına yardımcı olur. Argon gazı bu işlemlere yardımcı olduktan sonra sıvı ergimiş çeliğin içerisinden kalıp döküm tozlarının arasından geçerek ortamdan uzaklaşır. Argon gazı akış modelini etkilemektedir.
Gazın üflenmesinin arttırılması veya baloncuk ölçülerinin küçültülmesi akış düzenindeki değişikliği arttırmaktadır. Baloncukların büyümesi ile gaz daha kolay yüzmeye başlamakta ve kolayca kalıbı terk ederek akış düzenine daha az etki yapmaktadır. Küçük baloncuklar ise katılaşan kabuğun içine kaçma ihtimali olduğu için istenmeyen bir durumdur. Argon gazı eklenmesi döküm makinası içerisindeki süper ısının kaçışını hızlandırır ve geniş yüzey ve menisküs bölgesine daha çok ısının gitmesine sebeb olur. Buda yüksek ısı transfer noktalarını azaltır.