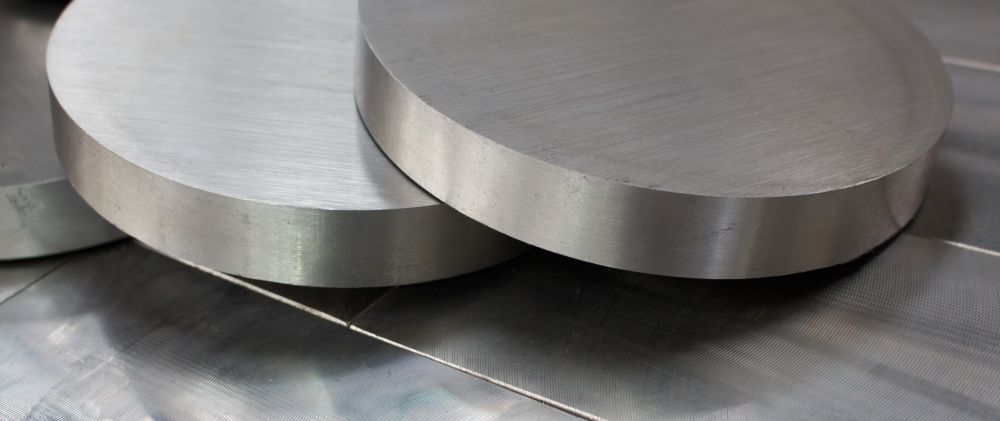
Hidrojen Şarj Koşullarında Dubleks Paslanmaz Çeliklerin Kırılma Tokluğuna Gerinim Hızı ve Mikro Yapının Etkileri
Hidrojen kaynaklı stres çatlaması (HISC) nedeniyle ferritik-östenitik paslanmaz çeliğin arızaları çok maliyetli olmuştur ve bazıları çözülmemiş olan denizaltı sistem bütünlüğü ile ilgili endişeleri artırmıştır. HISC çatlağı başlatma duyarlılığı, östenit aralığı ile güçlü bir korelasyon gösterir ve düz numuneler üzerinde yapılan testler, dövme parçalarda olduğu gibi büyük östenit aralığına sahip kaba taneli mikro yapıların, HISC'ye ince taneli yapılardan daha duyarlı olduğunu göstermiştir, örn. boru. Bildirilen tüm arızalarda, kaynaklar tipik olarak mevcut olmasına ve harici stres yoğunlaştırıcılarda başlatılmasına rağmen, çatlama imalat kusurlarının varlığından bağımsız olmuştur, bu nedenle kusurların önemi belirsizliğini korumaktadır. Hidrojen varlığında dubleks paslanmaz çelikteki kusurlara uygulanabilir kırılma tokluğu değerlerini belirlemek için iyi kurulmuş bir yöntem yoktur ve bu nedenle güvenilir veriler mevcut değildir, bu da kusurların kritikliğinin ve ince östenit aralığının herhangi bir fayda sağlayıp sağlamadığının anlaşılmamasına yol açar. kusurların genişlemesine karşı direnç. Bu makale, katodik polarizasyon altında deniz suyunda aktif şarj altında ürün tipi/mikroyapısı ve gerinim hızının kırılma tokluğu üzerindeki etkisini araştırmak için dubleks boru ve dövme ana malzemeler üzerinde gerçekleştirilen kırılma tokluğu testlerinden yeni veriler sunmaktadır. Bu, hidrojen yükleme koşulları altında kusur toleransını değerlendirmek için bir mühendislik kritik değerlendirme (ECA) yaklaşımının geliştirilmesine yönelik devam eden çalışmanın bir parçasıdır.
Tanıtım
TWI, DNV, Sintef ve diğer kuruluşların ortak çabaları, DNV Tavsiye Edilen Uygulama RP-F112'ye dahil edilen bir dizi ferritik-östenitik malzemenin HISC'ye direnci hakkında veriler üretmiştir. Bu belge, Foinaven manifoldundan süperdupleks göbek malzemesi üzerinde yapılan tam ölçekli testlerin sonuçlarıyla karşılaştırılarak doğrulanmıştır.
HISC konusunda bugüne kadar yapılan çalışmaların çoğu, HISC'nin başladığı stres ve gerinim seviyelerinin belirlenmesi ile ilgili olmuştur. İster yuvarlak çekme ister çentikli dikdörtgen numuneler olsun, deniz suyunda katodik korumalı (CP) küçük ölçekli sabit yük testleri, dubleks ve süper dubleks malzemelerin çatlak başlangıcı açısından HISC duyarlılığını karakterize etmek için kullanılmıştır. Bu duyarlılığın östenit aralığı ile güçlü bir korelasyona sahip olduğu ve testler kaba taneli mikro yapıların HISC'ye daha duyarlı olduğunu göstermiştir. Foinaven alanından göbek malzemeleri üzerinde yapılan sabit yük, çekme HISC testleri, süperdupleks malzeme %0.5'lik bir ilk gerilime yüklenirse, çatlakların çok hızlı bir şekilde başlayacağını ve yayılacağını gösterdi, ancak başarısızlık önemli ölçüde daha yüksek bir gerinimde meydana gelebilir. düşük sıcaklık sürünmesinin sonucu. Tam ölçekli göbekler üzerinde yapılan testler, çatlaklar bir kez başladığında, uygulanan yükte daha fazla artış olmadan yaklaşık 10 gün içinde yaklaşık 15 mm kalınlıkta yayılabileceğini gösterdi.
Bu ve sonraki araştırmalar, dubleks ve süper dubleks denizaltı bileşenlerinin hizmete uygunluğunun yeniden değerlendirilmesine yol açmıştır. Bildirilen tüm arızalarda, çatlama, üretim kusurlarının varlığından bağımsız olmuştur. Bununla birlikte, özellikle yüzey kırılması olmayan ancak hizmette uzun bir süre boyunca hidrojenin yayılabileceği fabrikasyon kusurlarından kaynaklanan arıza riskinin değerlendirilmesi, büyük, karmaşık yapılarda kusurlardan arındırılmasının sağlanması imkansız olduğundan gereklidir.
Önerilen Makale: Çelik profil malzemeler ve uygulamaları hakkında detaylı bilgi almak için
ıpe çelik profil fiyatları sayfamızı ziyaret etmenizi tavsiye ederiz.
Ancak, hidrojenin ve dolayısıyla güvenilir verilerin varlığında dubleks paslanmaz çelikteki kusurlara uygulanabilen kırılma tokluğunu belirlemek için iyi kurulmuş bir yöntemin olmaması, DNV-RP-F112'deki gibi potansiyel olarak çok muhafazakar yaklaşımların benimsenmesine yol açmıştır. Bu, pratik deneyimle çelişen görünen hidrojen şarj koşulları altında kusurların tolere edilemeyeceği anlamına gelir. Bu tür yaklaşımları geliştirmek, çatlak benzeri üretim kusurlarının davranışının daha iyi anlaşılmasını gerektirir ve deniz altı dubleks ve süper dubleks bileşenlerin güvenli ve ekonomik çalışması için çok önemlidir.
Servis sırasında katodik korumaya maruz kalmaktan dolayı yüksek düzeyde hidrojen içeren süper dupleks kaynak metali üzerinde havada gerçekleştirilen kırılma tokluğu testleri, tokluğun yüksek hidrojen içeriklerinde ve düşük gerinim oranlarında azaldığını ve gerinim hızının etkisinin çok düşük hidrojene kadar devam ettiğini göstermiştir. seviyeleri, düşük sıcaklık sürünmesinin bir etkisi olduğunu düşündürür. Bu makale, aktif şarj koşulları altında test edilen dubleks boru ve dövme ana malzemelerinin kırılma tokluğu hakkında yeni veriler sağlar ve özellikle gerinim hızının etkisini vurgular. Makale ayrıca, kırılma tokluğunun, pürüzsüz numunelerde çatlak başlangıcı için strese benzer şekilde ostenit aralığından etkilenip etkilenmediğini incelemektedir.
Deney
Malzemeler
İki tür malzeme test edildi:
Malzeme A, 12” dış çapa ve 12 mm et kalınlığına sahip %22 Cr dubleks paslanmaz çelik (UNS S31803) boru bölümüydü. Östenit aralığı 31μm
Malzeme B, %22 Cr dubleks paslanmaz çelikten (UNS S31803) bir dövme parçasıydı. Ostenit aralığı 44μm
Ostenit aralığı, testten sonra numuneler üzerinde çatlak ilerlemesi yönünde bir çizgi kesme yöntemi kullanılarak ölçülmüştür. Dört alan analiz edildi ve her alanda dört konum ölçüldü.
Kırılma Tokluğu Testleri
Testler, sekiz tek kenar çentikli büküm (SENB) numunesi üzerinde gerçekleştirilmiştir. Bir test havada 20°C'de, önceden hidrojen yüklenmemiş olan A malzemesinden Numune A-01 üzerinde gerçekleştirilmiştir. Diğer yedi test, SCE'ye karşı 1100mV'de katodik polarizasyona (CP) maruz bırakılarak testten önce (ve sırasında) hidrojenle yüklenen numuneler üzerinde 4°C'de doğal deniz suyunda gerçekleştirilmiştir. Yedi numune, A malzemesinden dört numune (A-02 ila A-05) ve B malzemesinden üç numune (B-01 ila B-03) içeriyordu.
Test numuneleri boru/dövme eksenine paralel olarak çıkarıldı ve bu eksene dik olarak çentiklendi ve yorulma ön çatlaması yapıldı. Nominal B değeri 12 mm olan bir kare (B°B) kesitine sahiptiler ve BS 7448:Bölüm 1'e göre hazırlandılar (işleme ve yorulma ön-çatlaması dahil). hidrojen yüklemesi veya testi (yükleme hızı dahil), bu değişkenlerin bir aralığı dikkate alındı. Üç numune (A-01, A-02 ve B-03), BS 7448:Bölüm 1 gibi standartlarda belirtilen sınırlar dahilinde gerilim yoğunluk faktörü (K) oranları veren yer değiştirme oranları altında test edilmiştir. Diğer numuneler daha düşük yer değiştirme altında test edilmiştir. Oranları (standart olmayan K oranları vererek) bu parametrenin kırılma tokluğu üzerindeki etkisini belirlemek için.
Fraktografi
Testten sonra kırılma yüzeyleri temizlendi ve bir taramalı elektron mikroskobunda (SEM) incelendi, başarısızlık mekanizma(lar)ını karakterize etmek ve bunları malzemenin mikro yapısı, hidrojen içeriği ve test gerilme oranı ile ilişkilendirmek için.
Metalografik bölümler
Ek olarak, çatlak yolunu mikroyapısal özelliklerle ilişkilendirmek için numunelerin kırılma yüzeylerinden metalografik kesitler çıkarıldı. Standart metalografik teknikler kullanılarak hazırlandılar ve 0.2g/NH4CNS ile %20 sülfürik asit kullanılarak dağlandılar. İlgili özellikleri kaydetmek için mikrograflar alındı.
Sonuçlar
Kırılma Tokluğu Testleri
Test ortamı (Numune A-01: hidrojen şarjı olmayan hava; diğer tüm numuneler: 1100mV potansiyel altında test öncesinde ve sırasında hidrojen şarjlı deniz suyu)
Ön Şarj Süresi (testten önce hidrojen ile şarj süresi)
Numune yüzeyine bitişik olarak alınan 1,6 mm kalınlığındaki bir dilimde ölçülen hidrojen içeriği. Bu değer, numuneler ön şarj edilmeden önce önceden çatlatıldığından, yorulma öncesi çatlak ucunun önündeki hidrojen içeriğini temsil eder. Hidrojen içerikleri, numuneler birlikte önceden doldurulduğundan ve test edildiklerinde birer birer çıkarıldığından değişiyordu.
CTOD (çatlak ucu açıklığının yer değiştirmesi) ve J (J integrali) cinsinden ifade edilen kırılma tokluğu sonuçları
Tüm testlerde, CTOD ve J sonuçları maksimum yük değerleridir (yani °m/Jm olarak sınıflandırılır ve test sırasında ulaşılan maksimum yükte kırılma tokluğunu temsil eder). A boru malzemesi (ostenit aralığı 31µm) için, standart bir yer değiştirme hızı altında havada test edilen ve hidrojen-olmayan numune A-01 (°=0.85mm, J=1403N/mm) için en yüksek kırılma tokluğu elde edildi. ücretli. En düşük sonuç boru malzemesi için elde edilmiştir, hidrojen yüklü olan A-05 numunesi (°=0.03mm, J=22.0N/mm) boru malzemesi A numuneleri arasında en uzun ön yüklemeye ve dolayısıyla en yüksek hidrojen içeriğine sahiptir ( 8ppm) ve çok düşük (standart dışı) bir yer değiştirme hızı (0,002 mm/saat) altında test edilmiştir.
Dövme malzemesi B (ostenit aralığı 44µm) için en yüksek kırılma tokluğu, standart bir yer değiştirme hızı altında test edilen ve öncesinde hidrojen yüklü olan numune B-03 (°=0.30mm, J=361N/mm) için elde edilmiştir. ve test sırasında. En düşük sonuç dövme malzemesi için elde edilmiştir, hidrojen yüklü olan B-02 numunesi (°=0.03mm, J=19.9N/mm), uzatılmış bir süre nedeniyle B malzemesi numuneleri (13ppm) arasında ikinci en yüksek hidrojen içeriğine sahiptir. Ön şarj süresi ve en düşük yer değiştirme hızında (0,002 mm/saat) test edilmiştir.
Hidrojen yüklü numuneler ve hem boru malzemesi A hem de dövme malzemesi B için kırılma tokluğu sonuçları (CTOD ve J açısından), test yer değiştirme hızı azaldıkça azalır. Örneğin, A-02 ve A-03 numunelerinin sonuçları, aynı hidrojen ön şarjı ve hidrojen içeriği süresi için, yer değiştirme oranını yaklaşık 70 faktör azaltmanın kırılma tokluğunda önemli bir azalmaya yol açabileceğini göstermektedir, 8-12 faktörü ile. Benzer şekilde, dövme malzemesi B için kırılma tokluğu sonuçları, test yer değiştirme oranı üç büyüklük mertebesi kadar düşürüldüğü için yaklaşık 10-20 faktör azalmıştır.
Kırılma tokluğu testlerinin sonuçları, yer değiştirme hızına karşı CTOD (δm) cinsinden,0.006 mm/saat'ten daha düşük yer değiştirme hızlarında, tokluk değerlerinin yer değiştirme (veya gerinim) hızı ile önemli ölçüde değişmediği görülebilir. Ayrıca, bu kadar yavaş gerinim oranlarında hidrojen içeriğindeki orta dereceli değişikliklerin malzemenin tokluğunu önemli ölçüde etkilemediği de açıktır. En önemlisi, çok düşük gerinim oranlarında dövme malzemesi B (44 µm ostenit aralığı) ile karşılaştırıldığında boru malzemesi A'nın (31µm ostenit aralığı) kırılma tokluğu performansları arasında hiçbir ayrım yapılamaz.
Fraktografi
A-01 (havada test edilmiş) ve A-02 (CP ile test edilmiş) boru numunelerinin sırasıyla şarjdan kaynaklanan 2ppm artık hidrojen ve 6ppm hidrojen içeren ve her ikisi de mikro boşluk birleşmesinden oluşan geleneksel bir gerinim hızı altında test edilen kırılma yüzleri, çeşitli boyutlarda mikro boşluklara sahip (birkaç mikrondan yaklaşık 50 um çapa kadar). Bu morfoloji, sünek bir kırılma mekanizması ile tutarlıdır. Yüklü numune A-02'nin, test edilen tüm numuneler arasında en kısa ön yüklemeye sahip olduğu not edilir.
6ppm hidrojen içeren ve CP altında ve düşük bir gerinim hızında (0.30mm/saat) test edilen boru numunesi A-03'teki kırılma yüzü, yaklaşık 100µm çapında ve çıkıntıları olan fasetlerden oluşuyordu. Bu morfoloji, hidrojen destekli çatlama için yaygın olarak gözlemlenen yarı-klevaj kırılma mekanizması ile tutarlıdır. Sırtlar muhtemelen ostenit adalarına tekabül etmektedir. CP altında çok düşük gerilme hızlarında (sırasıyla 0,006 ve 0,002 mm/saat) test edilen ve sırasıyla 6 ve 8 ppm hidrojen içeren A-04 ve A-05 boru numunelerindeki kırılma yüzleri, Şekilde gösterilenle karşılaştırılabilir morfolojiler sergiledi. 2, ancak daha kaba yüzeylerle (çap olarak birkaç yüz mikrona kadar).
Dövme numunesi B-03, en uzun ön yüklemenin bir sonucu olarak 17ppm ile en yüksek hidrojen konsantrasyonuna sahipti ve standart bir gerinim hızı altında test edildi. Kırık yüz morfolojisi, yaklaşık 100 um genişliğinde olan mikro boşluk birleşme ve yarı bölünme fasetlerinin bir karışımıydı.
Metalografik Bölümler
A boru malzemesindeki mikro yapı, bir ferritik matris içinde (borunun uzunluğunu takip eden) uzatılmış östenit tanelerinden oluşuyordu. Daha ince ve daha eş eksenli östenit taneleri de görülebiliyordu, ikincisi muhtemelen nihai çözelti ısıl işlemi sırasında oluşuyordu, oysa kaba östenitin hizalanması, şekillendirme sırasında mevcut olduğunu gösteriyor. A-01 ve A-02 boru numunelerinin standart, nispeten yüksek gerinim oranında test edilen kırılma yüzü profilleri, çatlak ucunun önünde plastik deformasyon kanıtı içeriyordu. östenit fazları. Kırık yüzlerinde yapılan SEM gözlemleri ile tutarlı olarak, kırık yüz üzerinde ve bitişiğinde mikro boşluk oluşumu gözlemlenmiştir.
Hidrojen yüklemesi ile test edilen A-03 ila A-05 boru numunelerindeki ve B-01 ve B-02 dövme numunelerindeki kırılma yüzlerinin profilleri büyük ölçüde benzerdi. Daha önce açıklanan profillerin aksine, çoğunlukla düzdüler ve mikro boşluklar yoktu. Çatlak hem ferrit hem de östenit fazları boyunca ilerlemiştir, ancak kırılma yüzeyinin profili ağırlıklı olarak ferritte düz ve düzdür, ancak östenitte değildir. Plastik deformasyon belirtisi görülmedi. B dövme malzemesindeki birincil östenit adacıkları, boru malzemesi A'dakinden daha iriydi ve kaba birincil östenit taneleri dövme işleminde daha eş eksenliydi.
B-03 dövme numunesindeki kırılma yüzeyinin profili, standartta test edildi, CP altında daha yüksek gerinim oranı, önceki her iki numune grubuna benzerlik gösterdi, yani A-01 ve A-02 boru numunelerinde görüldüğü gibi mikro boşluklar, A-03 ila A-05 boru numunelerinde ve B-01 ve B-02 dövme numunelerinde görüldüğü gibi daha yüksek gerinim hızında ve düz yarı yarılma fasetlerinde test edilmiştir. B-03 dövme numunesindeki metalografik kesit, esas olarak mikro boşluklardan oluşan kırılma yüzünün bir alanından alınmıştır. Bununla birlikte, karışık kırılma modu nedeniyle, bu bölüm daha yarı yarılma fasetleri olan bir alandan alınmış olsaydı, kırılma yüzünün profili muhtemelen B-01 ve B dövme numunelerinde gözlemlenen profille karşılaştırılabilir olurdu.
Tartışma
Kırılma Tokluğu Sonuçları
Yer Değiştirme Oranının Etkisi
Yer değiştirme hızı azaldıkça daha düşük kırılma tokluğu elde edildi ve yer değiştirme hızının etkisi çok yavaş yer değiştirme hızlarında (δ0,006 mm/saat) azaldı. Bu gözlem, boru numuneleri A-04 (°=0.03mm, J=23.3N/mm) ve numune A-05 (°=0.03mm, J=22.0) için kırılma tokluğu sonuçlarına dayanmaktadır; sonraki numune, önceki numuneden üç kat daha düşük bir yer değiştirme oranı altında test edildi. Benzer şekilde, B-01 dövme numunesi (°=0.03mm, J=22.7N/mm) için elde edilen kırılma tokluğu sonuçları, B-02 dövme numunesine (°=0.03mm, J=19.9N/mm) çok yakındır. ikincisi de öncekinden üç kat daha düşük bir yer değiştirme oranı altında test edilmiş olsa da. Ayrıca, en düşük yer değiştirme hızı (A-05 ve B-02) altında test edilen numunelerin her ikisinin de, daha uzun ön şarj ve test süreleri (A) nedeniyle biraz daha yüksek yer değiştirme oranı altında test edilen numunelerden daha yüksek hidrojen içeriğine sahip olduğunu belirtmekte fayda var. -04 ve B-01). Bu, yer değiştirme hızının düşürülmesinin (0,002 mm/saate) kırılma tokluğu üzerinde önemsiz bir etkiye sahip olduğunu gösterdiğinden (A-04 ve B-01 numuneleri için 0,006 mm/saatte elde edilen sonuçlarla karşılaştırıldığında) önceki sonucu güçlendirmektedir. daha yüksek hidrojen içeriği. Yaklaşık 0.02/mm/saatlik bir değer tahmin edilebilmesine rağmen, kırılma tokluğunun gerinme hızından büyük ölçüde bağımsız hale geldiği yer değiştirme oranını belirlemek için 0.006 ila 0.3 mm/saat aralığındaki yer değiştirme hızlarında ek testler gerekecektir.
Bununla birlikte, yukarıdaki sonuçların, belirli bir miktarda çatlak uzamasından sonra kırılma tokluğunu temsil eden tek noktalı maksimum yük sonuçlarına (yani, °m/Jm olarak sınıflandırılan sonuçlar) atıfta bulunduğuna dikkat edilmelidir. Yer değiştirme hızının kırılma tokluğu üzerindeki etkilerinin ve bunun çatlak uzamasına bağımlılığının daha kapsamlı bir şekilde anlaşılması, direnç eğrilerinin, bu çalışmanın kapsamı dışında olan bir dizi yer değiştirme hızı ve hidrojen yükleme koşulları altında belirlenmesini gerektirir.
Standart Yer Değiştirme Hızı Altında Hidrojen İçeriğinin Etkisi
Nispeten yüksek bir yer değiştirme oranı altında test edilen A-01 ve A-02 boru numunelerinin sonuçlarının karşılaştırılması, daha yüksek hidrojen içeriğinin olduğunu gösterir. A-02'de bu gerinim hızında kırılma tokluğu üzerinde önemsiz bir etkiye sahipti (Numune A-02 için CTOD ve J, hidrojenle yüklenmemiş A-01 için elde edilenlere çok yakındır). Standart yer değiştirme oranları altında elde edilen bu sonuç, boru malzemesi A için geçerlidir, ancak biraz daha kalın östenit aralığına sahip olan dövme malzemesi B için zorunlu değildir. B dövme ile ilgili tüm testler hidrojen yüklü numuneler üzerinde gerçekleştirilmiştir ve yalnızca bir test (numune B-03), boru numuneleri A-01 ve A-02 ile karşılaştırılabilir bir yer değiştirme hızı altında gerçekleştirilmiştir. Bununla birlikte, numune B-03 için kırılma tokluğu, numune A-01 ve A-02 için olanlardan önemli ölçüde daha düşüktü (δ=0.30mm, J=361N/mm). Bunun, B-03 numunesinin önemli ölçüde daha yüksek hidrojen içeriğine (17ppm) ve/veya A-01 ve A-02 numunelerine göre daha kaba bir mikro yapıya sahip olmasından kaynaklanıp kaynaklanmadığı bilinmemektedir. Büyük ihtimalle hidrojen içeriğinden kaynaklanmaktadır.
Düşük Yer Değiştirme Hızı Altında Hidrojen İçeriğinin Etkisi
0.006 mm/saat'ten daha düşük yer değiştirme oranları için, hem boru hem de dövme malzemeleri için kırılma tokluğunun, hidrojen içeriğindeki orta dereceli değişikliklerden büyük ölçüde etkilenmediğini göstermektedir (boru malzemesi A için 6 ila 8 ppm ve dövme malzemesi B için 7 ila 13 ppm). ), farklı ön şarj ve test sürelerinden kaynaklanmaktadır. Çok farklı seviyelerde hidrojen içeren numuneler üzerinde düşük yer değiştirme oranları altında hiçbir test yapılmadığından, yani 6 ppm'nin oldukça altında veya 13 ppm'nin oldukça üzerinde, mevcut sonuçların mevcut testlerde dikkate alınanların dışındaki hidrojen içerikleri için geçerli olup olmadığı bilinmemektedir. Yavaş gerinim hızı koşulları altında, test sırasında CP'den gelen hidrojenin, yüksek yerel gerilimler ve yayılan çatlak tarafından oluşturulan taze bir yüzeyin varlığı tarafından yönlendirilen, çatlak ucunda yüksek bir seviyeye konsantre olmak için yeterli zamana sahip olması muhtemeldir. Bu, malzemedeki "yoğun" hidrojen konsantrasyonunun kırılma tokluğu üzerinde (bu konsantrasyonlarda) neden sadece önemsiz bir etkiye sahip olduğunu açıklar.
Mikro Yapının Etkisi
0.006 mm/saat'ten daha düşük yer değiştirme hızları için, boru malzemesi A (östenit aralığı 31µm, numuneler A-04 ve A-05) ve dövme malzemesi B (ostenit aralığı 44µm ancak daha kalın bir birincil ostenit yapısı, numuneler B-01 ve B-02). Bununla birlikte, mevcut çalışmanın nispeten sınırlı kapsamı göz önüne alındığında, aynı gözlemin daha geniş bir mikro yapı aralığı için geçerli olup olmadığı bilinmemektedir, örneğin ince duvarlı boru/tüpte bulunanlar gibi <10 µm'lik çok ince östenit aralıklarına kadar, veya çok kalın duvarlı ürünlerde veya tüm gerinim oranları aralığında, örneğin standart (daha yüksek) yer değiştirme oranlarında olduğu gibi, >70 um çok kalın aralıklar. Pürüzsüz çekme numunelerinde çatlak başlangıcı için gerilim ve gerinmenin, bu östenit aralığı aralığında önemli ölçüde değişmediği belirtilmektedir.
Mevcut malzemelerde görülen kaba ve ince östenit karışımları ile ilgili olarak, ölçülen toplam östenit aralığının (farklı birincil östenit yapılarına rağmen) ve iki ürün formu için ölçülen tokluğun benzerliği, ince östenitin belirlenmesinde bir rol oynadığını göstermektedir. ince eş eksenli östenitin HISC üzerinde hiçbir yararlı etkisi olmadığı yönündeki önceki bir önerinin aksine, hidrojen yüklemesi altında tokluk.
Etkileri
Nispeten düşük kırılma tokluğu sonuçları, δ=0.03mm ve J = 20N/mm, hidrojen içeriği 6ppm veya daha yüksek olan numuneler için, test, test sırasında aktif şarj ile ve düşük yer değiştirme oranları altında, örneğin 0,006 mm'den az olduğunda gerçekleştirilmiştir. /saat. Düşük kırılma tokluğu değerleri, CP altında deniz altı uygulamaları için kullanılan dubleks ve süper dubleks bileşenlerde ölçülebilir herhangi bir yüzey kusuruna izin verilmemesi yönündeki mevcut endüstri uygulamasını desteklemektedir. Bunlar, belirli bir miktarda çatlak uzamasından sonra kırılma tokluğunu temsil eden maksimum yük sonuçlarıdır. Sonuçların nispeten düşük yer değiştirme oranları altında elde edildiği göz önüne alındığında, sabit yüklere veya çok düşük gerinim oranında uygulanan yüklere maruz kalan denizaltı bileşenlerinin değerlendirilmesi ile ilgilidir. Sonuçlar, çatlak ucunun yaklaşık 1,6 mm ilerisine kadar malzemede yaklaşık 6 ppm hidrojen içeren hidrojen yüklü malzemeler için kırılma tokluğunu temsil eder. İdeal olarak, kırılma tokluğu, direnç eğrileri cinsinden belirlenmelidir, çünkü bunlar, değerlendirmenin, çatlak uzamasının başlangıcındaki tokluk kullanılarak yapılmasına veya alternatif olarak, çatlak uzamasının itici kuvvet üzerindeki etkisini içeren bir yırtılma analizinin yapılmasına izin verir. Bununla birlikte, çatlak uzamasının zamana ve gerinime bağımlı olduğu malzemeler için bu tür direnç eğrileri oluşturmak kolay olmaktan uzaktır ve daha fazla araştırma gerektirir. Numune geometrisinin (esas olarak çentik yüksekliğinin numune genişliğine oranı) ve yükleme tipinin (yani eğilme ve gerilim) kırılma tokluğu üzerindeki etkisini değerlendirmek için ek araştırmalar da gereklidir.
Fraktografi ve Metalografi
Kırılma yüzeylerinde görülen fasetlerin ferrit fazı boyunca yayıldığı, sırtların ise ostenit ile ilişkili olduğu gözlendi. Öte yandan, kırılma yüzünün görünümünün sünek bir kırılma mekanizmasını (yırtılma) gösterdiği yerde, her iki fazda da mikro yapının deformasyonu ve mikro boşluk oluşumu gözlendi.
Yırtılma kanıtı, yalnızca standart (geleneksel) bir gerinim hızı altında test edilen numunelerde görülebilir. Bununla birlikte, en yüksek hidrojen içeriğini (B-03) içeren numunedeki kırılma mekanizması, muhtemelen testin geleneksel, daha yüksek bir gerinim hızında gerçekleştirilmesi nedeniyle, yırtılma ve gevrek mekanizmaların bir karışımıydı.
Ayrıca, CP altında ve kırılma tokluğu standartlarında belirtilen değerden daha düşük bir gerinim hızında test edilen tüm numuneler, yalnızca yarı bölünme fasetleri içeren kırılma yüzleri sergiledi. Bu numunelerdeki hidrojen miktarı (6 ila 13 ppm) kırılma yüzünün morfolojisini etkilemiyor gibi görünüyordu, ancak daha önce tartışıldığı gibi, bu muhtemelen daha yavaş gerinim hızı koşulu için test sırasında CP'den hidrojenin serbest mevcudiyetinden kaynaklanmaktadır. .
İki malzeme, yani boru ve dövme, dövme malzemesinde yarı yarılma yüzeylerinin boyutunun daha kaba olması dışında, düşük gerinim oranları altında test edildiğinde tutarlı kırılma tokluğu sonuçları ve kırılma yüzü morfolojileri sergiledi. Bu muhtemelen dövme malzemesindeki birincil östenit adalarının daha az hizalanmasını yansıtır, ancak daha büyük yüzey boyutunun daha düşük tokluğa dönüşmemesi ilginçtir. Bu nedenle, bu durumda malzeme tipinin, düşük gerinim oranları altında kırılma tokluğu değerlerini önemli ölçüde etkilemediği görülmüştür. Bununla birlikte, standart (geleneksel) gerinim oranı için kesinlikle benzer bir sonuca varılamaz, çünkü hiçbir boru malzemesi karşılaştırılabilir ön yükleme süresi ve dolayısıyla hidrojen içeriği ile test edilmemiştir, ancak CP altında geleneksel gerinim hızında test edilen boru numunesi önemli ölçüde daha yüksek tokluğa sahip olmuştur.
Özet
Bu çalışmada test edilen dubleks paslanmaz çelikler için, katodik koruma ve düşük yer değiştirme (veya gerinme) oranlarından kaynaklanan hidrojen, hem yarı yarılma mekanizmasıyla çatlak uzamasını teşvik etti hem de daha düşük kırılma tokluğu değerleri ile ilişkilendirildi.
Uygulanan gerinim oranı azaldıkça kırılma tokluğu azalır. Bununla birlikte, yer değiştirme hızının kırılma tokluğu üzerindeki etkisi, çok yavaş gerinim hızlarında azalıyor gibi görünmektedir ve CTOD veya J'nin yer değiştirme hızına karşı eğrisi, yaklaşık 0.02-0.006 mm/saatlik bir yer değiştirme hızında bir platoya ulaşır.
Standart yer değiştirme oranları altında, östenit aralıkları sadece orta derecede farklı olmasına rağmen (sırasıyla 31 ve 44 um) daha ince taneli boru ve daha iri taneli dövme malzemeleri için hidrojen yüklü numunelerde belirlenen kırılma tokluğu arasında önemli bir fark vardı. Bununla birlikte, hidrojen içeriğinde de büyük bir fark olduğu için, sonuçlardaki fark, en azından kısmen hidrojen içeriğinden kaynaklanıyor olabilir.
İnce taneli boru malzemesi A için en düşük kırılma tokluğu sonuçları °m=0.03mm ve Jm =22,0N/mm olmuştur. Bunlar, boru numuneleri (8ppm) arasında en uzun ön yüklemeye ve en yüksek hidrojen içeriğine sahip numune için elde edildi ve nispeten çok düşük (standart dışı) bir yer değiştirme hızı (0,002 mm/saat) altında test edildi.
Dövme malzemesi B için, en düşük kırılma tokluğu sonuçları °m =0.03mm ve Jm =19.9N/mm idi. Bunlar, dövme numuneleri (13ppm) arasında en uzun ikinci ön yüklemeye ve ikinci en yüksek hidrojen içeriğine sahip bir numune için elde edildi ve en düşük (standart dışı) yer değiştirme hızında (0,002 mm/saat) test edildi.
Çok düşük gerinim oranlarında, malzeme tipi, yani boru veya dövme ve ilgili mikro yapılar, mikroyapısal kabalık aralığının sınırlı olduğu kabul edilmesine rağmen, kırılma tokluğu üzerinde fark edilir bir etkiye sahip değildi. Bununla birlikte, yarılma yüzeyleri, daha iri taneli dövme malzemesi için daha büyüktü ve daha kaba birincil östenit yapısını yansıtıyordu.