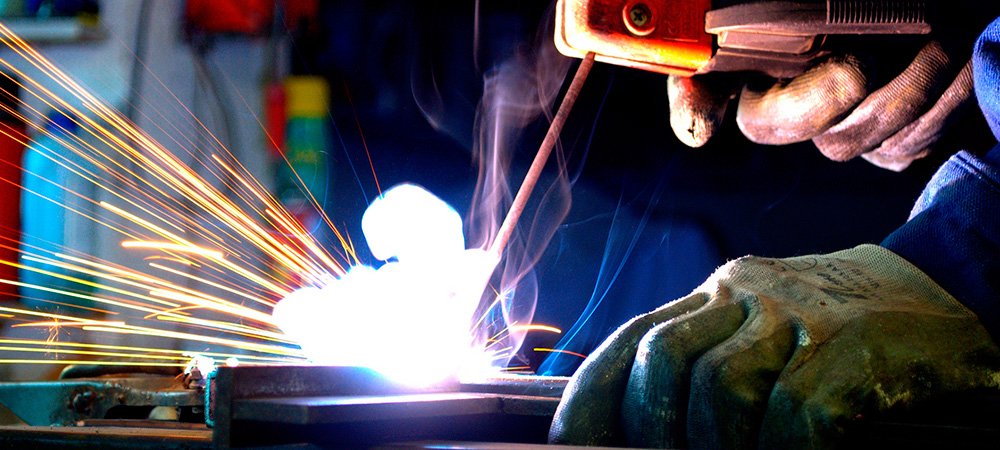
Paslanmaz çelik ve orta karbonlu çelik gibi iki farklı malzeme kaynak edildiğinde ısıl denge, ya yüksek dirençli paslanmaz çelik tarafındaki elektrot temas alanını artırarak ya da düşük karbonlu çelik tarafında daha yüksek dirençli elektrot kullanılarak sağlanır.
Genel olarak yukarıdaki şartlar, aynı malzemeden mamul fakat farklı kalınlığa sahip iş parçalarının kaynağı için de geçerlidir. Farklı kalınlıktaki metallerin kaynağında, yüksek kalınlık oranlarında, soğutulmuş elektrotun ince parça tarafında ara yüzeye daha yakın olması nedeniyle, ara yüzeyde yetersiz ısı üretimine doğru eğilim vardır. Uygun ısıl denge, ince iş parçası tarafında daha küçük temas alanına sahip elektrot kullanarak daha yüksek akım yoğunluğu elde etmek ve kısa kaynak zamanı kullanmak sureti ile gerçekleştirilir.
Burada ısıl denge durumunu etkileyen faktörler:
a. Kaynak edilecek malzemelerin izafi ısıl ve elektriksel iletkenlikleri
b. Kaynak edilecek parçaların izafi geometrileri
c. Elektrotların ısıl ve elektriksel iletkenlikleri,
d. Elektrotların geometrileri.
Soğuk Deformasyona Uğramış Farklı Malzemelerin Nokta Direnç Kaynağı
Soğuk deformasyona uğrayan farklı malzemelerin özellikle farklı paslanmaz çelik sacların birbirleri ile birleştirilmeleri, endüstride sıkça rastlanan bir durumdur. Sac levhaların birleştirilmelerinde en sık rastlanan yöntem de direnç kaynağıdır. Örneğin mutfak eşyalarından östenitik paslanmaz çelik tencereler ekstrüzyon işlemine tabi tutularak imal edilmektedirler. Deformasyona uğramış gövdelere ferritik paslanmaz çelik sac ve tutamaçların birleştirilmesi ihtiyacı ortaya çıkmaktadır. Kaynak işlemindeki termal sürecin derecesine bağlı olarak soğuk deformasyonla dayanım kazandırıldıktan sonra birleştirilen farklı paslanmaz çeliklerin ısı tesiri altındaki bölgesinde ve kaynak bölgesinde yapısal başarısızlıklar ortaya çıkabilir.
Önerilen Makale: Çelik profil malzemele ve uygulamaları hakkında detaylı bilgi almak için
çelik profil sayfamızı ziyaret etmenizi tavsiye ederiz.
AISI 304 – AISI 430 paslanmaz çeliklerin nokta direnç kaynak kalitesine, malzemenin kaynak öncesi farklı oranlarda maruz kaldığı soğuk deformasyonun etkisinin belirlenmesine çalışılmıştır. Farklı paslanmaz çelik çifti temin edildiği halde ve farklı oranlarda (%5, %10, %15) soğuk deformasyonlara uğratıldıktan sonra 7 kA akım şiddetinde 35 çevrim kaynak zamanında, 7 bar elektrot baskı kuvveti uygulanarak birleştirilmiştir. Kaynak kalitesini değerlendirmek için birleştirmenin mikro yapısı incelenerek, çekme makaslama yükü taşıma kapasitesi ve sertlik profili belirlenmiştir. Birleştirmenin mekanik özelliklerinin birleştirilen malzemenin şekil alabilirliğine bağlı olduğu bulunmuştur.
Tane irileşmesi nedeniyle tokluktaki azalmadan dolayı şekillendirilebilirliğin önemli olduğu yerlerde ferritik paslanmaz çeliklerin kaynaklı birleştirilmesi çok istenen bir durum değildir. Kimyasal bileşimlerinde kromun yanı sıra nikel de bulunan, kaynak edilebilirlikleri iyi olan ve endüstride geniş kullanım alanına sahip çelikler ise östenitik paslanmaz çeliklerdir. Tane sınırlarında krom karbür çökelmesi ile taneler arası korozyon oluşumu, kaynaklı birleştirmelerinde karşılaşılan önemli bir sorundur.
Endüstride kullanılan paslanmaz çelikler fabrikasyon uygulamalarında soğuk plastik şekillendirmeye maruz kalırlar. Soğuk plastik şekillendirme, malzemenin dayanım ve sertliğini artırır, çalışma sertleşmesi olarak da bilinen bu olay, dayanım artırma mekanizmalarından biridir. Ancak çeliklerin kırılmaya karşı dayanımının önemli parametrelerinden olan şekillendirilebilirlik, çalışma sertleşmesinden olumsuz etkilenir.
Soğuk şekillendirme ile kazanılan mukavemet ve sertlik artışı, termal süreçlerden olumsuz etkilenir. Kaynaklı birleştirmeler de termal süreç içerdiği için malzemenin mikro yapısının ve özelliklerinin önemli derecede değiştiği sıcaklık aralıklarında çalışma sertleşmesi ile kazanılan özelliklerde bir değişim olması kaçınılmazdır. Bu durum, kaynaklı birleştirmelerin yeniden kristalleşme ve tane büyümesi görülen ısı tesiri altındaki bölgesinin ana metalden daha zayıf olmasına sebep olmaktadır.
Yüksek Mukavemetli Çelik Sacların Düşük Karbonlu Çelik Saclara Nokta Direnç Kaynağı
0,8 mm eşit kalınlıktaki sacların üç eşit nokta kaynaklı bağlantısının düzlemsel eğmeli yorulma deneyi sonuçlarıdır. Yüksek mukavemetli çelik sacların bağlantısının (J–1) yorulma mukavemeti, düşük karbonlu çelik sacların bağlantısından (I–1) daha yüksek olduğu görülmektedir. Düşük karbonlu ile yüksek mukavemetli çelik sacların birleşimi olan bağlantının (K–1) yorulma mukavemeti, (I–1) ile kıyaslandığında, düşük tekrar sayısında yaklaşık aynı oldukları fakat tekrar sayınsın artması ile farkın arttığı gözlemlenmektedir. (K–1) bağlantılarında kırılma düşük karbonlu çelik saclarda yorulma oluşması sonucunda ortaya çıkmaktadır.
Kaynak edilmemiş yorulma mukavemeti çeliğin mikro yapısına ve mukavemetine bağlıdır. Kaynakla birleştirilmiş parçalarda ise durum daha karmaşık bir yapıdadır. Yorulma mukavemetini etkiyen parametrelerin (kaynağın neden olduğu bölgesel değişim, kaynağın geometrisi, kaynak hatalarının bulunuşu) hepsi gerilme birikimini artırırlar. Bu durum yorulma çatlağının başlamasını ve ilerlemesini kolaylaştıran koşullar oluşturur.
Nokta Direnç Kaynağında Karşılaşılan Güçlükler
Konstrüksiyon ve Geometri
Nokta direnç kaynağı genel olarak, aynı bileşimde ve aynı kalınlıktaki metal levhaların birleştirilmesinde kullanılır. Bununla beraber, ikiden fazla metal levhanın, bileşimi ve kalınlıkları farklı metallerin veya başka bir metal ile kaplanmış saçların birleştirilmesinde de kullanılabilir. Gaz veya su sızdırmazlığı istenmeyen, pres ile şekillendirilmiş parçalardan oluşan birleşik parçalar, yüksek bir üretim hızıyla, en ekonomik şekilde, nokta direnç kaynağı ile birleştirilebilirler. Nokta direnç kaynağının en önemli avantajları, yüksek hızlı olması, yüksek imalat kapasitesindeki birleştirme hatlarında kolaylıkla kullanılabilmesi ve otomasyona elverişli olmasıdır. Akım, zaman ve elektrot kuvvetinin otomatik kontrolü ile yüksek imalat hızlarında, sağlam ve birbirinin aynı özellikte nokta kaynaklan elde edilebilir. Ancak nokta direnç kaynağı genel olarak yaklaşık 3 mm. kalınlığa kadar olan saç levhaların birbiri üzerine bindirilerek birleştirilmesinde çok geniş bir uygulama alanına sahiptir. Çok yaygın olmamakla birlikte 12 mm kalınlığa kadar sacları bu yöntemle kaynatmak mümkündür.
Farklı pozisyonlardaki veya daha kalın parçaların birleştirilmesinde ise yetersiz kalmaktadır. Daha kalın parçalar için projeksiyon kaynağı uygun olabilmektedir.
Kaynak Bölgesindeki Isı Oluşumu ve Soğuma Hızı
Geniş bir uygulama alanı olan elektrik nokta direnç kaynağında, iş parçaları, ısı ve basınç enerjisi kullanılarak birbirlerine birleştirilir. En yüksek sıcaklık, parçalar arasındaki temas yüzeyindedir. Bu yöntemde, iş parçaları, lokal olarak çok hızlı bir şekilde ısıtıldığından, soğuma hızı çok yüksektir. Bu hızlı soğumanın etkisi ile iş parçalarının malzemelerinde bazı içyapı değişiklikleri oluşabilir. Bu nedenle, nokta direnç kaynağında, soğuma hızı ve sıcaklık dağılımı çok önemlidir. Kaynak bölgesindeki ısı oluşumunu etkileyen en önemli faktörler, malzemenin elektrik direnci, kontak direnci, basınç, levha kalınlığı, kaynak zamanı, gerilim ve akım şiddetidir.
Kaynak sırasında soğuma hızının sınırlandırılması gereken durumlarda, akım şiddetinin kontrol altında tutulmasının akılcı bir çözüm olacağını söylemek mümkündür. Örneğin, kaynak akımını bir anda kesmek yerine, akım kademeli olarak azaltılabilir (azalan akım kontrolü). Bu durumda, çok hızlı bir sıcaklık düşümü yerine, kontrollü ve yavaş bir soğuma hızı elde edilir; dolayısıyla mikro yapıda oluşabilecek değişimler en aza indirilebilir. Kaynak yapılan iş parçasının sıcaklığını yükseltip (ön tavlama), kaynak metali ile iş parçaları arasındaki sıcaklık farkını azaltarak da soğuma hızını yavaşlatma yoluna gidilebilir. Ancak bu ısıl işlemin direnç kaynaklarında kullanımı çok yaygın değildir. Çok kalın parçaların kaynağında, içyapıyı değiştirecek kadar yüksek sıcaklıkların oluştuğu bazı özel durumlarda, ön tavlama veya kaynak sonrası ısıl işlem uygulanabilir.
Isıl Dengenin Ayarlanması
Eğer eşit bileşimde ve kalınlıkta iki levha, eşit kütle ve şekle sahip elektrotlarla kaynak edilirse, ısı her iki parçada da üniform olarak üretilecek ve kaynak kesidi tipik oval bir biçimde olacaktır. Bu şart mevcut ise ısıl denge mevcuttur. Bununla beraber levhalardan biri diğerine göre daha yüksek elektrik dirence sahipse, ısı bu levhada diğerine nazaran çok daha hızlı üretilecektir. Bu nedenle yüksek elektrik iletkenliği ve dolayısıyla da yüksek ısı iletkenliğine sahip bakır, gümüş, alüminyum gibi metallerde yüksek akım yoğunluğunda bile üretilen çok az ısı çevreye hızla yayılır ve erime için gerekli ısı birikimini engeller. Bu ise kaynak işlemini imkansız veya zor hale getirir. Isıl dengenin mevcut olmadığı durumlarda, örneğin paslanmaz çelik ve orta karbonlu çelik gibi iki farklı malzeme kaynak edildiğinde, ısıl denge ya yüksek dirençli paslanmaz çelik tarafındaki elektrot temas alanı artırılarak veya düşük dirençli orta karbonlu çelik tarafında daha yüksek dirençli elektrot kullanılarak sağlanır. Bu açıdan bakıldığında, elektrot seçimi kritik bir konu olarak karşımıza çıkmaktadır.
Elektrotlar
Direnç kaynağında ısıyı yoğunlaştırma etkisinin oluşturulabilmesi için belirli bir başlangıç direncine ihtiyaç vardır. Malzeme sıcaklığının artması ile direnç artar¸ bu ısınmayı hızlandırır ve dolayısıyla sıcaklık çok kısa bir sürede lokal bir bölgede malzemenin ergime sıcaklığına yükselerek çekirdek oluşumu gerçekleşir. Yüzeydeki çinko tabakası veya ana metallerden birindeki çinko bileşimi iyi bir ergimenin sağlanabilmesi için gereken başlangıç direncini düşürür.
A ve B eğrileri başlangıç direncinin uygun ve yeterli olduğunu gösterirken, C eğrisi bu direncin düşük ve yetersiz olduğu durumları göstermektedir. Galvanizli çeliklerde, kaynak akımı daha yüksek olduğundan C eğrisi biraz daha yükselebilir. Grafiğin üst limiti sıçramanın başladığı durumu temsil ederken alt limit çok küçük ve yetersiz çekirdek çapını göstermektedir. Galvanizli çeliklerde veya elektrik iletkenliği yüksek metallerde daha yüksek kaynak akımları kullanıldığından elektrotların temas yüzeylerinde sıcaklık aşırı yükselerek bakır malzemenin sertliği azalır. Diğer yandan bu durum çok hızlı bir şekilde boyutları kabul edilemez derecede küçük kaynak çekirdeklerinin oluşmasına neden olur. Ayrıca bakır malzemenin sertliğinin azalması, elektrotların yüzeye yapışmasına, temas yüzeylerinin deforme olmasına ve genişlemesine sebep olur.
Galvanizli çeliklerde çinko tabakasının yanmasının elektrotların yüzeyine bir etkisi daha vardır. Mükemmel bir direnç kaynağında elektrotlar içerisinden geçen akımın mümkün mertebe sabit olması gerekir. Sadece kaynak akımının yüksek olması değil aynı zamanda çinko tabakasının ergime sıcaklığının düşük olması da bu durumu büyük ölçüde etkilemektedir. Elektrolitik olarak yapılan çinko kaplama tabakası yaklaşık olarak 420°C’ ergir. Sac metal ise 1400°C’ye kadar ısındığı için ilk aşamada çinko tabakası yanar ve bakır elektrotların üzerine yapışır, bu noktalarda elektriksel direnç artar. Bu metal yapışması elektrot yüzeyine genelde düzensiz bir dağılım gösterir ve özellikle elektrotların orta kısımlarında ya da çukurlaşan bölgelerinde yoğunlaşır. Bu durumun temas direncinde temas direncinde değişikliklere sebep olması sonucunda akım düzensiz akmaya başlar ve yetersiz büyüklükte kaynak çekirdekleri olan nokta kaynakları elde edilebilir.
Metal yapışması ve çukurlaşma gibi olaylar, halka kaynağı (çekirdeğin yetersiz çapta oluşması ve sacların sadece elektrotların diş kısımlarına gelen yerlerinden halka şeklinde birbirine kaynak olması) oluşma riskini ortaya çıkarmaktadır. Halka kaynaklarında çekirdeğin diş uçlarında ve bağlantı bölgesi içerisinde ilave bir çinko bağı oluşur. Bu bağ mekanik direncin artmasına sebep olur ve tahribatlı testlerde uygun şekilde hataların belirlenmesini engeller.
Bu bağ etkisinden dolayı keski ile ayırma metodunun güvenilirliği her zaman kuşkuyla karşılanmış ve ultrasonik testle kıyaslandığında kesinlikle daha az geçerliliği olan bir yöntem olarak düşünülmektedir.
Elektrotların çukurlaşmasının bir diğer sonucu da büzülme kavitasyonudur. Çinko tabakası yandığında yüksek basınç altında gaz kabarcıkları ve içi hava dolu boşluklar meydana gelir ve bunlar kaynak bölgesinde sac metal erir erimez yayılırlar. Elektrotların çukurlu şeklinden dolayı kaynak dış uçta şekillenir ve içe doğru gelişir. Bu tip bir şekillenmeden dolayı gaz kabarcıkları iç kısma doğru zorlanır. Sonuç olarak kaynak bölgesinde ve çoğunlukla da toplam kalınlığın ortasında büzülme boşlukları oluşur. Uzun kaynak zamanı gaz boşluklarının oluşması için yeterli zaman tanıdığından genellikle büzüme boşlukları genellikle daha kalın sacların kaynağında meydana gelir. Kaynak açısının sürekli değişmesi yukarıda ifade edilen etkileri azalttığından robot kaynak makineleri büzülme boşlukları konusunda bir avantaj sağlar.
Farklı ergime sıcaklıkları ve ısıl iletkenlik özelliklerine sahip farklı metallerin birleştirilmesinde yakma alın kaynak yöntemi ve sürtünme kaynak yöntemleri en uygun yöntemler olarak ön plana çıkmaktadır.
Farklı Metallerin Birleştirilmesinde Kullanılan Diğer Yöntemler
Gerek yakma alın kaynak metodunda gerekse sürtünme kaynağı metodunda, kaynağı gerçekleştirilecek parçaların eksenleri birbirlerine çakışık olmalıdır. Kaynak kalitesi açısından eksen kaçıklığı çok önemlidir ve bu konuda mümkün olabildiğince dar toleranslarda çalışılmalıdır. Bu toleransların sağlanması, elektrik iletkenliği yüksek ve parçalara nazaran yumuşak olan, bu yüzden de sık sık işlenmesi gereken elektrotlardan dolayı yakma alın kaynağında daha zordur. Sürtünme kaynağında ise bağlama aparatlarının iç kısmı sertleştirilmiş ve taşlanmıştır ve daha yüksek bir ömrü vardır. Dolayısıyla toleransların sağlanması daha çok mümkün olmaktadır. Sürtünme kaynağında dönel kesitlerin yanı sıra dörtgen kesitli parçalar da kaynaklanabilir. Yakma alın kaynağında ise bunlara ilaveten açılır kesitler ringler de kolaylıkla kaynaklanabilmektedir. Bununla birlikte yakma alın kaynağında kesitlerin özdeş olması gerekirken, sürtünme kaynağında farklı kesitler ( levha - çubuk gibi) kolaylıkla kaynak edilebilmektedir.
Kaynak öncesi yüzey hazırlığı, uygulanan dövme basıncından dolayı, her iki kaynak metodunda da kritik değildir. Ancak sürtünme kaynağında, sürtünme hareketinin yüzeydeki süreksizlikleri parçalayarak dışarı sürmesinden dolayı yakma alın kaynağında kaynak olayını etkileyebilen yüzey tabakaları, sürtünme kaynağına menfi bir etkide bulunmamaktadır. Yüzeyde bulunabilecek çizikler her iki kaynak metodunda da kaliteyi etkileyebilecek unsurlardır. Kaynak öncesi giderilmeleri gerekir.
Yakma alın kaynağında başka hiçbir kaynak yönteminde rastlanmayacak kadar çok parametre bulunmaktadır. Bu da kaynak metodu için optimum şartların sağlanmasını zorlaştırmaktadır. Sürtünme kaynağında da bir takım parametreler söz konusu olmasına rağmen yakma alın kaynağına nazaran daha az olması ve, optimizasyon için sadece temel kaynak parametrelerinin simülasyonunun yeterli olması ve bunların tamamının makine üzerine set edilebilmesi optimum kaynak şartlarının sağlanmasında yakma alın kaynağına nazaran avantaj sağlamaktadır. Bunun yanı sıra sürtünme kaynağı yakma alın kaynağındaki gibi elektrik akımından ve kaynak bağlantısındaki elektrik direncinden etkilenmemektedir. Yine optimizasyon içim önemli olan yakma alın kaynağındaki yakma prosesinin etkileri de sürtünme kaynağında söz konusu değildir.
Yakma Alın Kaynağı
Yakma alın kaynağı elektrik direnç kaynağının bir türü olup, ısı, dövme ve yığma işlemlerinden oluşur. Yakma alın kaynağının endüstriyel uygulamalarından biri de matkap uçlarının birleştirilmesidir. Maliyeti ve malzeme israfını önlemek için matkap uçlarının uç kısımları HSS’den, sap kısımları düşük karbonlu çeliklerden yapılır.
a) Parçaların çeneler arasına sıkıştırılması: Kaynak işlemi esnasında parçaları tam ölçüsünde tutan, kaynak akımını ve yığma kuvvetini parçalara ileten elemanlara elektrot veya germe elemanı adı verilmektedir. Germe elemanları akım geçirme özelliklerinden ötürü genellikle bakır ve alaşımlarından seçilmektedir.
b) Parçalara yakma geriliminin ve akımının uygulanması, kızak hareketinin başlaması.
c) Normal gerilimde yakma işlemi.
d) Yığma uygulanması ve akımın kesilmesi.
Yakma alın kaynak işlemi ön ısıtma, yakma ve yığma kademelerinde çok sayıda işlem parametresine sahiptir. Kaynak tasarımının kalitesini doğrudan etkileyen parametreler: Malzeme çapı, gerilim, akım, sayaç, ön ısıtma zamanı, yığma akım zamanı, yığma zamanı, sıkma basıncı, ilerleme basıncı, yığma yolu, yığma+yakma yolu ve kızak hızıdır.
Sürtünme Kaynağı
Sürtünme kaynağı yöntemi ile birleştirilecek metalsel malzemelerden bir tanesi döndürülebilen diğeri ise eksenel olarak kayma hareketi yapabilen iki sıkıştırma düzeneğine tutturulur. Birinci sıkıştırma düzeneği hızla döndürülürken ikincisi dönen yüzeye doğru hareket ettirilir. Kaynak parçaları temas ettiklerinde sürtünmeden dolayı ısınırlar. Ergime sıcaklığının hemen altında bir ısınma elde edildiğinde çevirme işlemi durdurulur ve parçalar büyük bir kuvvetle birbirlerine bastırılarak kaynamaları sağlanır. Bu işlem esnasında kaynak bölgesindeki malzeme sıkışma sonucu dışarı taşar.
Sürtünme Dikiş Kaynağı İle Farklı Metalsel Malzemelerin Birleştirilmesi
Başlıca yöntemlerle kaynak edilemeyen bir çok malzeme ve malzeme kombinasyonları sürtünme kaynak prosesi ile birleştirilebildiği için olan kaynağa uygunluğun belirlenmesindeki kriterler sürtünme kaynağında kullanılamazlar. Sürtünme kaynağı için uygunluk şartları;
a. Malzeme mukavemeti: Malzeme mukavemeti, sürtünme kaynağı sırasında eksenel basınç ve dönme momentiyle aşırı bir deformasyonun oluşumunu önleyecek kadar olmalıdır.
b. Sıcak şekil değiştirme kabiliyeti: Birleştirilecek metalsel malzemelerin yeterli düzeyde sıcak şekil değiştirebilir özellikte olması istenir.
Bu kriterleri yerine getiren pek çok demir ve demir dışı metaller sürtünme kaynağı ile kaynak edilebilirler. Sürtünme kaynağı farklı termik ve mekanik özelliklere sahip metallerin kaynağında da kullanılır ki genellikle bu malzemeler diğer kaynak yöntemleriyle kaynaklanamaz. Erime sıcaklığı altı sıcaklıklar ve kısa kaynak süresi sürtünme kaynağına bu imkânı vermektedir. Buna örnek olarak alaşımlı veya alaşımsız çeliğin alüminyum ve bakır ile toz metalurjisi ile üretilen parçaların ve seramiklerin alüminyum ile sert ve ağır metallerin diğer metallerle sürtünme kaynağı gösterilebilir.
Farklı termik ve metalik özelliklere sahip metallerin sürtünme kaynağı simetrik olmayan deformasyon miktarına yol açar. Yüksek bir kaynak mukavemeti ise rölatif olarak simetrik plastik deformasyon veren farklı malzemelerin kaynağında elde edilir.
Demir esaslı malzemeler, yumuşak çelikten yüksek alaşımlı çeliklere kadar kaynaklanabilmektedir. Yumuşak çelikler rölatif olarak daha kolay kaynaklanmakta ve geniş bir parametre aralığına sahiptirler. HSS türü yüksek alaşımlı çelikler ise daha dar bir parametre aralığında ve daha yüksek eksenel kuvvetlerle kaynaklanabilirler. Bunların tokluğu ve çatlama hassasiyeti dikkat edilmesi gereken bir konudur. Parçalarda oluşan çapaklar muhakkak alınmalıdır çünkü bu çapaklar çatlak başlangıcı için uygun yerlerdir.
Paslanmaz çelikler verilen kaynak parametrelerinde kolaylıkla kaynaklanabilirler. Isıl işlemli paslanmaz çelikler diğer yüksek alaşımlı paslanmaz çelikler gibi kaynak değişkenlerine karşı çok hassastırlar ve ITAB arzu edilen özellikler için kaynak sonu prosesler gerektirir. Bunun dışında sinterlenmiş malzemeler, Al ve alaşımları, Cu ve alaşımları, Ti ve alaşımları, Zr ve alaşımları, Mg alaşımları, ısıl direnci yüksek Ni ve Co alaşımları, refrakter metaller olan T, Mo, Ni alaşımları da sürtünme kaynağı ile kaynaklanabilmektedirler.
Projeksiyon Kaynağı (Kabartılı Kaynak)
Projeksiyon kaynağı, nokta direnç kaynağının bir türevidir. Düşük karbonlu çelikler, düşük alaşımlı çelikler, paslanmaz çelikler, nikel ve bakır alaşımları bu yöntemle uyumlu malzemelerdir. Alüminyum ve titanyum yüzeylerinde oluşan oksit tabakası nedeniyle bu yöntemle kaynak edilemez. Oksit filminin ergime derecesi alüminyumdan yüksektir. Paslanmaz çelik ve nikel esaslı malzemelerinde yine yüzeylerinde oluşan oksit filmi nedeniyle kaynak edilmeleri güç olacaktır.
Nokta direnç kaynağı ile birleştirilemeyecek kalınlıktaki malzemeler bu yöntemle birleştirilebilirler.
Kabartıların 0.075 mm civarında kontrol edilmesi gerekir.
Noktasal temas tepecikleri üzerinden birleşme sağlandığından gerekli kuvvet ve akım değerleri nokta direnç kaynağına nazaran düşüktür. Bu yöntemle her çeşit uygulama için düz elektrotlar kullanılabilir.
Nokta direnç kaynağından farklı olarak bu yöntemde herhangi bir ergime söz konusu olmayan katı hal birleştirme yöntemidir.
Bu işlemin kısıtlaması ise, kabartıların elde edilmesiyle ortaya çıkan ilave işlemlerdir. ‘Kuvvet destekli difüzyon bağı’ olarak nitelendirilir.